실리케이트 유리의 전열물성 및 윤활기능 최적화 및 몰드플럭스로의 활용
Controlling the Thermal and Rheological Properties of Silicate Glasses for Development of Advanced Mold Flux Systems
Article information
Trans Abstract
Development of the advanced mold flux is always mandatory to enhance both the quality and productivity of continuous casting of steels. Especially, the increasing demands for high alloy steels production and high speed casting reveals serious contradiction between two principal functions of mold flux: lubrication and controlling heat transfer. In order to overcome this problematic needs, some innovative research activities are being carried out. MAE (Mixed Alkali Effect) has been examined in alumino-borosilicate-based mold system to stabilize alkali cation and aluminum association, which enables chemically stable glassy mold flux film during casting of high alloy steels. Non-Newtonian mold fluxes could be developed by addition of Si3N4 or SiC due to the increase of stiffness of polymeric structure, which would be beneficial to satisfy the contradictory requirements of viscosity at mold top surface and mold wall. Some innovative ideas for controlling mold heat transfer without deteriorating the lubrication have been examined by dispersion of nano-size metallic particles and by modification of prenucleation motif. All these trials are closely related with glass science and engineering. Therefore, it should be highly beneficial to enhance the collaborative research activities between glass and metallurgy society for further development of advanced functional mold flux systems.
1. 서론
현 재 철 강 재 료 의 응 고 는 대 부 분 연 속 주 조 (continuous casting)공정을 통하여 이루어진다. 정련 (refining)을 마친 용강은 레이들 (ladle)이라는 용기에 담겨서 턴디쉬 (tundish)를 거쳐 주형 (mold)으로 주입된 후 주형 벽면에서 냉각되어 응고된다. 고로 (blast furnace)에서 주형에 이르기까지 모든 공정단계에서 용강 (molten steel)은 슬래그 (slag)와 같이 공존하게 되며, 각 단계별로 적절한 성분의 슬래그로 용강의 성분을 제어하는 기술이 적용되고 있다. 다른 슬래그와는 달리, 주형에서 사용되는 몰드플럭스 (mold flux)는 용강 성분제어 이외에도 특수한 기능을 수행하게 된다. 그림 1에서 주형은 적절한 주기로 진동하며, 응고쉘은 일정한 주조속도로 주형 아래쪽으로 이동하므로, 주형과 응고쉘 사이에는 마찰력이 발생하게 된다. 몰드플럭스는 주형 진동에 의하여 주형과 응고쉘 사이로 유입되어 필름형태를 유지하면서 마찰력을 줄이는 윤활기능을 갖추어야 한다. 또한 주형 내에서는 응고쉘의 두께가 크지 않아서 열전달계수 (heat transfer coefficient)가 지나치게 커질 우려가 있다. 이 경우 응고쉘에 가해지는 응력 및 변형률이 지나치게 커져서 크랙을 유발하게 되므로, 몰드플럭스 필름은 적절한 전열저항도 갖추어야 한다. 우수한 윤활기능 및 전열제어기능을 갖추기 위하여 몰드플럭스는 일종의 글래스세라믹 (glass ceramic) 재료와 유사한 구조와 특성을 가지며 최적 설계를 위하여 유리공학 (glass engineering) 관점에서의 접근이 활발하게 이루어지고 있다. 1930년대 Junghans [1]에 의하여 최초로 주형진동에 의한 금속 연속주조 공정이 구현된 이후, 철강 응고 시 생산성과 품질은 몰드플럭스의 성능에 의하여 크게 영향을 받게 되었다. 특히 고강도, 고합금강 개발이 급격하게 진행되면서 몰드플럭스의 성능에 대한 요구사항은 더욱 엄격해지고 있다. 본 논문에서는 몰드플럭스 다양한 물성을 최적화하기 위하여 이루어진 최근의 연구성과를 유리공학적 관점에서 살펴보고자 한다.
2. 몰드플럭스의 구조와 조성
2.1. 주형 내 몰드플럭스 조성 및 형상
몰드플럭스는 주형에 도포되어 용강의 현열에 의하여 용해된 후 주형 진동에 의하여 주어지는 동압 (dynamic pressure)에 의하여 주형과 응고쉘 사이로 유입되어 필름형태로 존재하게 된다. 몰드플럭스 필름 두께 분포에 대한 수치해석 [2–4] 및 모사실험 [5–6]에 의하면 주형 내 몰드플럭스 필름의 두께는 초기 유입부에서는 1-3mm 이며 점차 얇아져서 주형 하단에서는 0.5mm 이하이다.
그림 2 [7] 는 실제 조업 중인 주형에서 채취한 슬래그필름으로, 분산된 커스피다인 (cuspidine: Ca4 Si2 O7 F2) 결정을 갖는 글래스세라믹 구조임을 알 수 있다. 결정상은 윤활기능과 전열제어 기능을 적합하게 하기 위하여 구형으로 분산하여 제어한다. 필름 내 유리질은 윤활기능을, 분산된 결정상은 전열제어가능을 각각 향상시키게 된다. 몰드플럭스의 성분계는 아래 예와 같이 CaO-SiO2-CaF2-Na2 O 4원계로 이루어지며 여기에 MgO, Al2 O3, B2 O3 등이 일부 첨가된다. CaO, SiO2, CaF2는 커스피다인 결정을 형성하는 주요 성분이며, 적절한 유리질을 확보하기 위하여 CaO/SiO2 중량비는 일반적으로 0.5-1.5 범위로 유지한다. 그림 3의 CaO-SiO2-CaF2 3원계 상태도에서 [8] 결정상은 커스피다인이 거의 유일하므로 주형 내 몰드플럭스 필름의 윤활능 확보에 유리하다. 만약 여러 종류의 결정상이 주형 내에서 형성된다면 결정상이 서로 연결되어 유효점도가 급격하게 증가하므로 윤활기능이 악화되므로 적절하지 않다. 다만, CaO-SiO2-CaF2-Na2 O 계에서도 액상의 몰드플럭스가 주행 내로 유입된 후 커스피다인 결정상이 생겨나면, 잔류하는 glass melts 내에는 SiO2 함량이 높아져서 유효점도가 급격이 상승할 우려가 있다. 따라서 몰드플럭스에는 공업적으로 사용하기 적합한 알칼리산화물인 Na2 O를 첨가하여 잔류 유리질의 점도를 낮추도록 설계한다. 그림 4는 상업용으로 설계된 몰드플럭스의 점도를 열역학 database인 FactSage로 평가한 사례이다. 결정화를 일으키지 않고 과냉된 경우 (푸른색)에 비하여 결정상을 정출한 경우 (붉은색)의 잔류 glass melts의 점도가 더 낮아지게 되어 윤활능 확보에 유리하다. 이상과 같이 몰드플럭스는 조성은 적절한 형상의 필름을 형성하도록 설계되며, 경험칙에 근거한 설계 사상은, 1) 단일한 결정상 형성, 2) 결정상 생성 후 잔류 glass melts 의 점도 하향, 3) 결성상이 서로 군집되지 않도록 미세하고 분산된 결정형상 유지, 등으로 요약할 수 있다.
2.2. 사면체구조 안정성
이상적인 몰드플럭스 필름 구조를 유지하기 위하여 적절한 비율의 결정상과 함께 잔류 유리질을 유지하여야 하므로, 연속주조 주형 내 고온에서의 사면체구조를 안정적으로 유지하여야 한다. 조성 및 온도에 따른 사면체구조를 평가하기 위하여, 종래의 CaO-SiO2-CaF2 계 몰드플럭스에서는 아래 식 1의 준화학반응 (Quasi Chemical Reaction)을 고려하여 산소음이온의 존재형태 별 분포를 예측하는 방법을 사용한다.[9]
위 식에서 O0, O−, O2-는 각각 가교산소 (Bridging Oxygen), 비가교산소 (Non-bridging Oxygen), 자유산소 (Free Oxygen)을 의미한다.
각각의 준화학반응의 열역학적 평형으로부터 산소 분포를 구한 후, 더욱 구체적인 사면체구조를 예측하는 방법은 이항분포 [10]를 가정한 간단한 예측방법으로부터, Lagrange최적화 [11], 사슬구조를 가정한 1차원 polymer가정 [12] 등이 제시되었다. 하지만 각각의 방법은 모두 지나친 단순화를 전제로 하므로 향후 분자동력학 계산 등의 방법과 병행하여 보다 체계적인 모델 개발이 필요하다.
최근 Al, Ti 등 SiO2를 쉽게 환원시킬 수 있는 합금성분을 다량 함유한 고합금, 고강도강 생산이 널리 확대되고 있다. 이 경우 주형 탕면에서의 급격한 화학반응으로 인하여 몰드플럭스의 성분이 대폭 바뀌어서 적절한 유리질 함량을 유지하기가 어렵게 된다. [13, 14]
이에 따라, Al2 O3를 다량 함유한 CaO-Al2 O3-SiO2-CaF2를 주성분으로 하는 새로운 몰드플럭스 성분계를 개발하여 고합금강 주조 시에도 화학적 안정성을 확보하려는 연구가 폭 넓게 시도되었다. [15–24] 기존의 성분계와는 달리 Al2 O3를 다량 함유한 몰드플럭스에서는 고온에서의 AlO4어지는 문제점이 있다. [19] 그림 5는 CaO-Al2 O3-SiO2-4- 사면체의 구조적 안정성이 급격히 떨 B2 O3-CaF2 성분계 몰드플럭스를 대상으로 과냉된 액상을 각각 610℃ 및 1210℃에서 급냉하여 제조한 유리를 NMR (핵자기공명분광기)로 구조분석한 사례이다. 저온에서는 비교적 AlO44- 사면체가 안정되게 존재하지만, 고온에서는 사면체구조가 분해되어 Al2 O3가 8면체구조로 바뀌면서 염기성산화물 (network modifier)로 작용함을 알 수 있다.
실제 연속주조 공정에서 Al2 O3사면체를 갖는 몰드플럭스를 적용할 경우 고온에서의 사면체 구조 분해로 인하여 지나치게 많은 결정상이 생성되어 윤활기능을 잃어버리게 된다. [15–19] 이를 극복하기 위한 방안 중 하나로, 혼합알칼리 효과 (MAE: mixed alkali effect)를 활용하는 방안이 제시되었다. [25] 혼합알칼리 효과는 Li, Na, K 등 상이한 원자간 포텐셜을 갖는 양이온들을 혼합함으로써 유동성 (mobility)를 억제하는 효과이다. 실리케이트 유리에서 혼합알칼리 효과에 의한 점도증가 및 전기전도도 감소효과가 널리 보고되었으나 (예를 들어 [26]), Al2 O3계 유리형성능을 향상시키는 데어도 활용 가능함이 규명되었다. 그림 6은 CaO-Al2 O3-SiO2-B2 O3-CaF2 조성계에서 Li2 O Na2 O, K2 O를 단독 혹은 섞어서 총 19 mole% 첨가하여 용해한 후 1400℃에서 급냉한 결과이다. 단일 알칼리 산화물을 추가하였을 때에는 앞의 그림 5에서 언급한 것 처럼 고온에서의 AlO44- 사면체의 불안정성 때문에 급냉 조건에서도 대부분 결정질로 존재하였지만, 2종의 알칼리산화물을 첨가하였을 때에는 혼합알칼리 효과에 의하여 유리형성능이 현저히 개선되었다. 향후 본 방법에 의한 새로운 몰드플럭스 설계 및 적용이 기대된다.
3. 몰드플럭스의 열물성
3.1. 몰드플럭스의 점도 예측 모델
몰드플럭스를 포함하여 여러가지 공업용 슬래그에서 점도는 가장 중요한 물성이다. 다량의 염기성산화물을 함유하는 몰드플럭스의 점도는 fragile한 특성을 가지므로 아레니우스 관계식으로 손쉽게 예측하기는 불가능하다. 경험식에 의거하여 슬래그의 점도를 예측하는 모델은 수정된 아레니우스 식을 기반으로 하며, Urbain model [27], Riboud model [28], Iida model [29] 등이 널리 활용되고 있다. 다양한 점도예측 모델에 관하여는 Jung 등이 [30] 잘 정리한 리뷰논문을 참조하기 바란다. 이러한 경험기반 모델은 폭 넓은 조성계에 적용하기에는 어려움이 따르므로, 필연적으로 구조기반 점도예측 모델 개발이 필요하다. 예를 들어 Kim [31] 등은 수정된 준화학모델 (Modified Quasi-chemical Model)을 기반으로 점성거동의 활성화에너지를 슬래그의 구조에 기반하여 평가하여 다양한 슬래그 및 유리성분계의 점도를 성공적으로 예측하였다.
3.2. 비뉴톤형 몰드플럭스
주형 벽면에서의 몰드플럭스 필름은 점도를 가능한 낮추는 것이 윤활능 확보 측면에서 유리하다. 하지만 지나치게 점도가 낮아지면 주형 탕면에서 액상의 몰드플럭스가 용강으로 혼입되는 현상이 발생한다. [32] 그림 7에서 보여지는 것처럼 액상의 몰드플럭스가 혼입되는 위치와 형태는 다양하지만, 공통적으로 외부에서 주어지는 에너지가 탕면의 액상 몰드플럭스의 점성유동를 일으키는 것에서 시작된다. 따라서 몰드플럭스의 점도는 적정 범위를 유지할 수밖에 없으므로, 결정상의 분율이 높아지거나 주조속도가 빠른 조업조건에서는 윤활기능이 충분하지 않게 된다. 이러한 모순점을 해결하기 위한 방안으로 비뉴톤형 점성유동 특성을 갖는 몰드플럭스 개발이 시도되었다. [33–38]
몰드플럭스 내에 사면체구조가 발달하여 네트워크를 형성하면 전단변형율 (shear rate)의 증가에 따라 점도가 감소하는 전단박화 (shear thinning) 현상이 나타나게 된다. 이러한 비뉴톤형 점성거동은 아래 식으로 정량화 할 수 있다.
위 식에서 flow behavior index (n)가 1이면 뉴톤형 점성거동을 일으키며, 1보다 낮아질수록 보다 강한 전단박화 특성을 갖는다. 이는 위에서 언급한 몰드플럭스 점도 설계의 어려움을 해소할 수 있는 방안이다. 즉, 탕면에서는 두터운 액상 몰드플럭스 층을 가지므로 외부에서 충격이 가해지더라도 최대 전단변형율은 10-40 (1/second) 정도로 비교적 낮게 유지된다. 반면 주형 벽면에서 필름형태로 윤활막을 형성할 경우 주형 진동에 의하여 주어지는 최대 전단변형율은 100-1000 (1/second)에 이르게 된다. [33] 따라서, flow behavior index가 가능한 낮은 몰드플럭스를 개발할 경우, 주형 탕면에서는 높은 유효점도를 갖게 되어 슬래그의 혼입을 방지할 수 있고, 주형 벽면에서는 낮은 유효점도를 나타내어 우수한 윤활기능을 유지하게 한다.
그림 8은 염기도 (CaO/SiO2 중량비) 1.0인 상업용 몰드플럭스를 기본 조성으로 하고, 여기에 다양한 첨가제를 추가하여 전단박화능을 조사한 결과이다. 기본조성에서는 flow behavior index가 0.874였으며 B2 O3 28wt% 첨가에 의하여 0.841, Si3 N4 1wt% 첨가 시 0.812, SiC 1wt% 첨가 시 0.786으로 각각 낮아졌다. 이러한 첨가제의 효과는 사면체 네트워크 발달 및 이로 인한 강성 (stiffness) 증가가 주된 원인이다. 즉 가교산소의 경우 2개의 사면체를 연결하게 되지만, 가교질소는 3개, 가교탄소는 4개의 사면체를 최대로 연결할 수 있으므로 전단변형에 저항하는 강성 (stiffness)가 증가하게 되고 이로 인해 전단박화 특성이 향상됨을 알 수 있다. 전단박화로 대표되는 비뉴톤형 점성특성은 차세대 고기능 몰드플럭스 설계에 유용하게 활용될 것으로 기대된다. 다만 Si3 N4 나 SiC와 같은 첨가제는 용융온도가 극히 높으므로 통상의 방법으로 균질한 조성의 몰드플럭스를 제조하기에는 어려움이 따르며 주형 탕면에서 용강과 접촉하는 경우 용강과 반응할 우려도 있기 때문에, 이에 대한 대응방안을 수립해야만 한다.
3.3. 금속분산 몰드플럭스의 열전도도
몰드플럭스 필름은 윤활기능과 함께 전열제어기능도 갖추어야 한다. 특히 주형 상부에서의 초기응고 단계에서는 응고쉘의 전열저항이 미미하기 때문에 지나치게 많은 열유속 (heat flux)이 발생할 가능성이 크다. 이 경우 열응력에 의하여 초기 응고쉘이 파단될 위험이 크므로 몰드플럭스 필름의 전열저항을 높여서 대처하게 된다. 몰드플럭스의 전열저항은 일반적으로 결정상의 분율이 높을수록 커지는 것으로 보고된다. 이는 분산된 결정상과 유리질 계면에서 photon scattering 이 발생하거나 결정화에 따른 부피수축으로 인하여 필름 표면에 요철이 생겨나서 계면 열저항이 발생하기 때문이다. [39–41] 따라서 크랙발생에 민감한 제품을 주조할 경우에는 결정상의 분율을 높여야만 하는데, 이로 인하여 윤활기능이 떨어지는 문제가 생겨난다. 이와 같이 몰드플럭스의 윤활기능과 전열제어기능은 서로 상충되는 경향을 나타낸다. 이를 해결하기 위한 방안으로 결정상을 함유하지 않으면서도 전열저항을 높일 수 있는 방안으로서 미세 나노금속 입자를 분산시킨 몰드플럭스 개발이 시도되었다. [42–45]
미세한 산화물을 저렴한 비용으로 제조하기 위하여, 염기도 (CaO/SiO2 중량비) 1.0의 몰드플럭스에 약 0.5wt%의 Fe2 O3를 첨가하고 B2 O3 함량을 6.5-28.1 wt%로 조절한 후 흑연도가니에서 용융시켰다. 비교적 낮은 염기도와 높은 B2 O3 함량으로 인하여 모든 몰드플럭스는 극히 유리형성능이 우수하여 결정질은 존재하지 않았다. 소량 첨가된 Fe2 O3는 용해 과정에서 흑연도가니와 반응하여 그림 9에 보여지는 미세한 크기의 Fe 입자를 형성하게 된다. 특히 B2 O3 는 Fe2 O3로부터 여분의 산소를 공여 받아서 사면체를 형성하므로 적절한 함량을 첨가하게 되면 Fe 입자의 생성을 촉진시키는 효과가 발생한다. [43] 본 실험에서는 9.3wt% B2 O3 첨가 시 (B2) 생성된 Fe 입자의 수가 가장 많았다. 그림 10은 해당 몰드플럭스의 photon 산란계수(scattering coefficient)를 나타낸 것이다. 금속입자 숫자가 높은 B2 몰드플럭스의 산란계수가 최대 2000/m 이상이어서 결정상을 형성하지 않으면서도 전열제어 기능을 충분하게 수행할 수 있음을 나타낸다. 이러한 산란거동은 Mie scattering 이론과 잘 부합하였다. 여기에 더하여, 몰드플럭스 내에 미세 분산된 금속입자는 phonon scattering도 일으킴이 최근의 연구에 의하여 확인되었다. [45] 종합하면, 수십~수백 나노미터 크기의 금속입자를 몰드플럭스 내에 분산시키면 photon과 phonon을 모두 산란시켜서 전도와 복사열전달을 모두 효과적으로 제어할 수 있으므로, 향후 결정상을 형성하지 않고 유리질로만 구성된 몰드플럭스로도 전열제어기능과 윤활기능을 우수하게 수행할 가능성이 기대된다.
4. 몰드플럭스의 결정화 제어
전술한 바와 같이, 몰드플럭스 필름의 전열제어 기능을 수행하기 위하여는 적절한 분율의 cuspidine 결정상이 필요하다. 이에 따라, 등온 (예를 들어 [46–48]) 및 비등온 (예를 들어 [49, 50]) 조건에서의 몰드플럭스 결정화 kinetics 연구가 활발하게 진행되어 왔다. 이를 통하여 규명된 주요한 사실은 몰드플럭스의 결정화 kinetics는 nucleation에 의하여 지배된다는 것이다. 그림 11은 비등온 방식으로 melt crystallization 단계에서의 활성화에너지를 Friedman 식으로 조사한 결과이다. 비등온 조건에서는 결정화 진행 단계에 따라 활성화에너지가 달라지는 점에 유의해야 한다. 그림 11에서 모든 몰드플럭스 시료의 모든 단계에서 몰드플럭스 결정화에 수반되는 활성화에너지는 음 (−)의 값을 나타내었다. 이를 그림 12의 개략도와 비교하면 음의 활성화 에너지를 갖는 구간 (Anti-Arrhenius region)은 핵생성속도가 전체 결정화속도를 지배하는 구간 임을 알 수 있다.
전술한 것처럼 고합금강 혹은 높은 주조속도의 연속주조 조업에서는 전열저항을 낮추어야만 주조재의 크랙발생을 막을 수 있다. 이를 위해 해당 조업용 몰드플럭스는 염기도를 높여서 결정상의 분율을 키우는 전략을 택하게 된다. 하지만 이로 인하여 결정화 kinetics, 즉 핵생성 속도가 지나치게 빨라지게 되면 슬래그 필름의 윤활기능이 악화될 뿐 아니라 필름의 유동자체가 제한되고 분단현상이 생겨나서 주형 내 열전달거동이 극히 불안정, 불균일하게 되고 결국 주편 표면에 깊은 크랙을 유발한다. 비교하자면 고합금강 및 고속주조 시 결정상 분율을 높이는 것은 자동차의 가속기능에 비교할 수 있다. 따라서, 자동차의 제동기능에 비교될 만한 몰드플럭스이 핵생성속도 제어방안 역시 반드시 필요하다. 이를 갖추기 위하여 고염기도 몰드플럭스에 Na2 O와 함께 Li2 O를 소량 첨가하여 핵생성 속도를 제어하는 설계방안이 시도되었다.
그림 13에 Li2 O첨가에 따른 비등온 조건에서의 몰드플럭스 결정화 거동 추이를 나타내었다. L0, L1, L2는 각각 기존의 Na2 O 함량을 유지하면서 추가적으로 Li2 O를 각각 0, 1, 2 wt% 추가하였음을 의미한다. 모든 냉각속도 조건에서 Li2 O 첨가에 다라 일관되게 결정화 거동이 지연되고 있음을 알 수 있다. 이는 몰드플럭스 내 사면체구조의 발달거동과는 반대되는 현상이다. 즉 Li2 O 첨가에 따라 사면체구조의 분해가 가속되지만 결정화 kinetics는 지연되고 있다. NMR 분광분석 [50] 및 분자동력학 계산 [51] 을 통하여, 그림 14에서 보듯이 Li는 F 와 강하게 결합함을 알 수 있었다. 비고전적 핵생성 이론에 따르면 결정핵 생성을 위하여는 결정화 이전단계에서의 전구체 (prenucleation motif)가 필요한데, 몰드플럭스에서 커스피다인에서는 CaF 결합이 이러한 전구체로 작용하게 될 것이다. 따라서 Li-F 결합이 형성되면 CaF 전구체 형성을 방해하게 되므로 결정화 kinetics를 적절하게 지연시킬 수 있게 된다. 이를 그림 15의 개략도로 나타내었다. 이와는 별도로 Li와 Na 양이온 들의 알칼리혼합효과 (mixed alkali effect) 역시 이러한 결정화 kinetics 지연에 영향을 끼칠 것으로 추정되므로 이에 대한 규명도 필요하다.
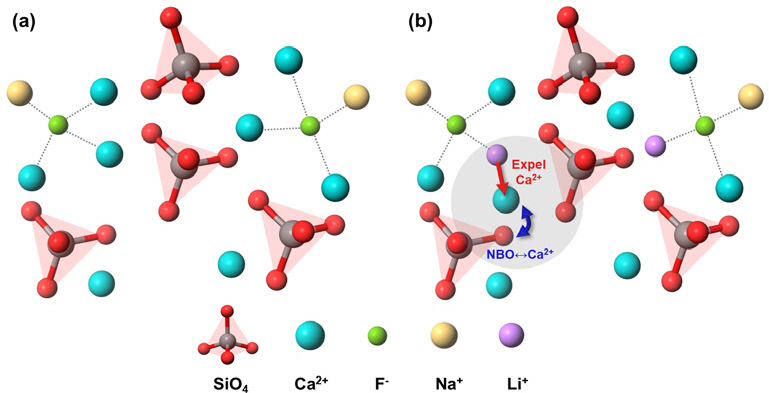
Schematics of structural changes in consideration of Li2 O incorporation. (a) without Li2 O (b) with Li2 O
몰드플럭스 구조에 대한 체계적인 이해를 바탕으로 핵생성거동 및 결정화 kinetics를 이해하고 제어하는 것은 보다 발전된 기능을 수행하는 몰드플럭스 개발을 위하여 반드시 필요하며, 향후 실험 및 계산과학을 활용한 연구가 활발하게 진행될 것을 기대한다.
5. 요약
1980년대 국내에 연속주조 공법이 도입된 이래, 몰드플럭스 기능의 발전은 연속주조 공정의 생산성과 품질 수준을 결정하는 인자로 자리잡게 되었다. 하지만 경험칙에 의거한 발전은 이제 한계를 나타내고 있으므로, 유리공학적 관점에서 몰드플럭스의 구조와 물성을 이해하는 것이 다음 단계의 몰드플럭스 기능 향상을 위하여 필요 불가결한 요소이다. 본 논문에서는 저자의 연구결과를 중심으로 최근의 몰드플럭스 기능향상을 위한 설계사례를 보고하였다. 몰드플럭스의 윤활기능 향상을 위한 점탄성거동, 전열제어 기능 향상을 위한 나노금속입자 분산 및 핵생성속도 제어 등은 고합금강 주조 또는 고속주조를 위한 차세대 몰드플럭스 개발에 적극 활용될 전망이다. 향후에도 몰드플럭스 개발을 위하여는 유리공학과 금속공학 분야를 망라한 협업이 필수적으로 수반되어야 할 것이다.
References
Biography
◉◉조중욱
◉ 1998년 일본 Tohoku Univ. 공학박사
◉ 1998년~2012년 포스코 기술연구원전문연구원
◉ 2012년~2016년 포스텍 철강.에너지소재대학원연구부교수
◉ 2016년~현재 포스텍 철강.에너지소재대학원 교수