서론 (Introduction)
질화규소(Silicon nitride, Si3N4)는 지각 내에 자연적으로 존재하지 않는 물질이기 때문에 반드시 합성을 통해서만 얻을 수 있는 세라믹 소재이다. 질화규소에 대한 첫 번째 보고는 1857년에 Wohler와 Deville에 의해 최초로 발견되었는데, 실리콘을 2중 도가니 안에서 반응시키되 탄소를 이용하여 산소를 제거함으로써 얻었다고 한다.[1] 1879년 용광로에서 실리콘을 브라스크(목탄, 석탄, 또는 코크스를 도가니를 깔때기 위해 사용되는 점토와 혼합하여 만든 페이스트)로 가열하여 얻은 테트라니트라이드, Si3N4의 조성을 가진 소재가 처음 보고되었으며, 1910년에는 Weiss 와 Engelhardt에 의해 순수한 질소 아래에서 실리콘을 가열하는 직접 질화법으로 질화규소가 최초로 합성된 바 있다. 1925년에 실리카(SiO2)를 질소 분위기 하에서 탄소환원 방식으로 1250–1300°C로 가열하여 질화규소를 만드는 방법도 보고되었다.[2,3]
질화규소의 생산공정/방법 및 결정학적 특성 등에 대한 광범위한 연구를 거쳐, 상업적으로 1950년대 전후 상업적 용도로 사용되기 시작하였다. 1948년부터 1952년까지, 미국의 Carborundum Company는 질화규소의 제조와 응용 분야에 대해 특허를 출원하였고[2], 그 후 Haynes (Union Carbide)社에서 열전대 튜브, 로켓 노즐, 금속 용해용 보트 및 도가니용으로 질화규소 부품 상업화에 성공하였다. 1971년, 미국 국방부 및 Ford, Westinghouse 는 질화규소 가스 터빈을 제조하기도 하였다.[4] 지난 70년간 질화규소의 낮은 열팽창계수, 높은 열전도율, 우수한 열충격성, 양호한 내산화성, 양호한 기계적, 광학적 특성으로 인해 첨단 세라믹 분야에서 중요성이 증가하고 있다. 그에 따라 질화규소의 전 세계 생산량은 오랜 기간 정체되어 있다가 최근 들어 고절연/고방열이 요구되는 분야에서 사용이 증가함에 따라 꾸준히 증가하는 추세이다.[5] 질화규소의 전 세계 생산량은 2012년 1,110 톤에서 2016년 1,500 톤로 증가하였고, 2023년의 추정치는 약 2000 톤으로 예상되고 있다.
1.1. 질화규소 결정상
질화규소는 세 가지 결정상 α, β, γ 상을 나타낸다. Vassiliou 등[6]과 Ruddlesden 등[7] 연구진에 의해 1957년, 1958년 각각 확인된 α 상과 β 상은 육방정 결정 구조를 가지고 있으나 원자 적층 구조 차이로 인해 격자상수는 다른데, α 상의 c축 격자상수가 β 상의 약 2배이다. 1999년에 보고된 γ 상은 입방정 스피넬 결정구조를 가지고 있다. α 상 및 β 상은 적당한 고온 및 상압 조건에서 생성될 수 있는 반면, γ 상은 초고압(>15 GPa) 및 고온(>1700℃)을 만족하는 조건에서만 생성될 수 있다.
α 상은 1200℃ 미만에서도 형성될 수 있는 저온 안정상 질화규소이고 β 상은 대략 1400℃ 이상에서 본격적으로 형성되는 고온 안정상 질화규소이다. 1400℃ 이상의 온도에서 열처리를 하게 되면 α 상은 비가역적으로 β 상으로 상변태되는데, 이러한 상변태는 각 단위격자에 존재하는 6개의 Si-N 결합이 파괴되고 재구성되는 과정이다. α-β 상변태 메커니즘은 액상이 존재하는 경우에만 진행될 수 있으며, 두 가지 결정상 모두 질화규소 생산 과정에서 존재하는 액상과 불순물에 따라 1200∼1400℃ 사이에서 공존할 수 있다. 또한, β-α 역방향 상변태는 불가능한 것으로 알려져 있다.
α 및 β-Si3N4의 기본 단위구조는 Si-N 가 구성하는 사면체 구조이다. 불규칙한 사면체의 중심에는 Si 원자가 위치하고, 모서리에는 4개의 N 원자가 연결되어 있고, 각각의 N 원자는 이웃하는 3개의 다른 사면체와 공유되고 있는 구조이다.
α 및 β-Si3N4 내의 Si-N 원자 간 결합은 모두 공유결합성이 높고 이온결합성이 낮다. 높은 공유 결합성은 Si 원자 4개의 sp3 오비탈이 N 원자의 sp2 오비탈과 중첩되기 때문에 기인하고, 각각의 N 원자는 고립 전자쌍에 의해 점유되는 비결합 p 오비탈을 가지고 있다.
β-Si3N4 구조는 Be 및 O 원자가 Si 및 N 원자로 대체된 광물 페나사이트(phenacite, Be2 SiO4)에서 유래되었다. α-Si3N4의 기저면은 ABCDABCD 순서로 적층되고, β-Si3N4의 경우는 ABABABAB 순서로 적층된다. AB 적층은 α-Si3N4와 β-Si3N4에서 동일한 반면, α-Si3N4의 CD층은 c-글라이드 평면에 의해 β-Si3N4의 AB층과는 다른 형태로 적층된다. Fig. 1은 [1120] 방향에서 본 α-Si3N4와 β-Si3N4의 적층 순서를 나타낸 것이고, 점선은 단위격자의 c축 방향으로 반복되는 것을 의미하며, 파란색과 녹색의 구는 각각 Si와 N 원자에 표시하고 있다. α 및 β-Si3N4에서 기저면에 평행한 N-Si3의 삼각형 결합 형태는 빨간색 삼각형으로 표시되어 있는데, 이 평면은 기본 단위의 육각형 배열을 8개의 원자가 구성하는 고리 형태로 가지고 있으며, 이는 기저 면에 1.5Å 직경의 공극을 만들어 준다. β-Si3N4의 경우 이러한 공극이 중첩되면서 연결되는 구조를 가지므로 결정상 내부에 채널을 형성하는 반면, α-Si3N4는 단위격자의 c축 방향으로 AB층 위에 CD층이 180˚만큼 회전하여 적층되는 구조를 가지기 때문에, 이로 인해 β-Si3N4와는 달리 채널 대신 포켓 형태의 공극이 생성된다.[8]
Fig. 1
질화규소 소재의 결정구조 (a) α 상 (b) β 상 (c) γ 상 (d) [1120] 방향에서 본 α-Si3N4와 (e) β-Si3N4의 적층 순서 Adapted from Kuwabara et al. Phy. Rev. B 2008;78:064104, with permission of the American Physical Society and SciPris [8]
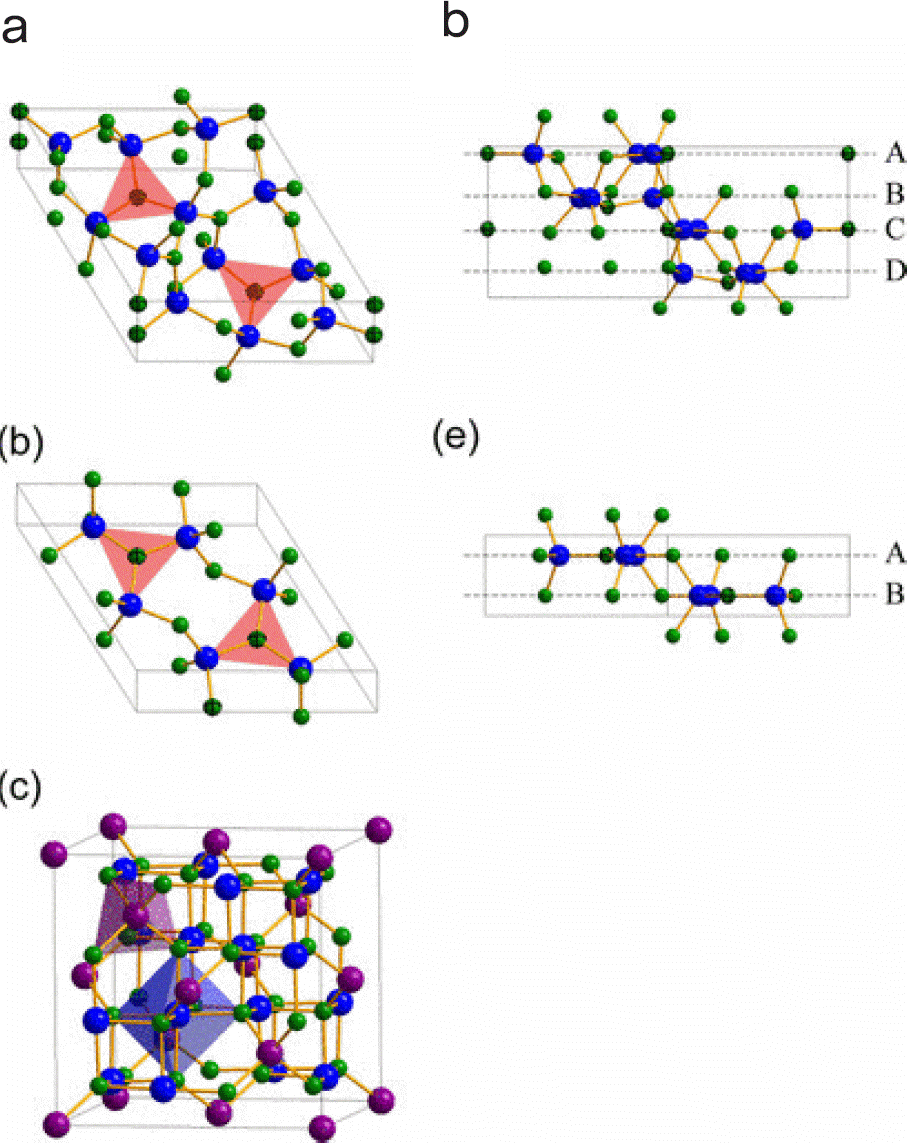
1.2 질화규소 분말 합성법
1.1 절에 언급하였듯이, 질화규소는 저온 안정상인 α 상과 고온 안정상인 β 두 가지 결정상으로 존재한다. 일반적인 제조방법을 사용하여 합성된 질화규소 분말은 소량의 β 상을 포함하거나 포함하지 않고 주로 α 상으로 구성되어 있으며, 소결첨가제와 함께 질화규소 세라믹을 액상 소결할 때 사용되는 출발 원료분말 또한 주로 α 상 질화규소이다. α 상 질화규소는 고온의 액상소결 과정에 따라 부분적으로 또는 완전히 β상 질화규소로 상변태 될 수 있는데, 질화규소 세라믹 제품의 품질은 초기 질화규소 원료분말의 특성에 따라 달라지기 때문에 원료분말의 특성이 매우 중요하다. 한편, 합성에 사용된 초기 실리콘 원료 출처에 따라 제조된 질화규소 원료분말의 형상, 불순물 함유량, 특성 등이 모두 달라질 수 있다[2]. 일반적으로 질화규소 분말은 아래와 같은 4가지 방법으로 제조될 수 있다.
-
• 실리콘의 직접 질화
(Direct nitridation of silicon) -
• 실리카의 탄소열 환원
(Carbothermal reduction and nitridation of SiO2, CRN) • 이미드 합성 (Di-imide synthesis)
-
• 연소 합성(또는) SHS 방법
(Combustion synthesis or SHS method)
Si를 직접적으로 질화하는 방법은 질화규소 분말을 제조하기 위해 가장 일반적으로 널리사용되는 방법이다. 직접 질화법으로 질화규소 분말을 제조하는 공정은 Si 분말의 질화, 분쇄 및 불순물 원소의 제거의 과정을 거친다. 질화규소 분말의 품질은 원료인 Si 분말의 순도, 입자 크기, 형태 및 표면적에 따라 달라지는데, 직접질화범에 사용되는 Si 분말은 일반적으로 저가의 야금 등급에서 고가의 반도체 등급까지 다양한 스펙트럼을 가진다. 통상적으로 질화 반응은 N2 분위기에서 수 시간에서 수 일 동안 1200-1500℃ 온도 범위에서 수행된다. 오랜 기간 질화 반응에 대한 연구개발 과정을 통해 NH3, N2/H2 또는 N2 분위기 하에서 촉매를 첨가하거나 첨가하지 않고 Si의 녹는점(1412℃) 이하의 온도에서 비교적 짧은 공정 시간(24시간 미만) 열처리를 통해 고품질 질화규소 분말 생산이 가능하다. H2 를 사용하는 이유는 Si의 완전한 질화를 촉진할 뿐만 아니라 질화 반응을 방해하는 O2의 분압을 제어할 수 있기 때문이다. Si 직접 질화는 높은 발열 반응(1400°C에서 약 725 kJ/mol)이기 때문에 이론적으로는 반응에 의해 온도가 수 백℃까지 상승 가능하므로 반응 생성물에서 Si 이 용융되어 미반응되는 현상을 피하기 위해 대부분 실리콘의 녹는점 아래에서 질화 공정이 진행된다. 질화 과정에서 실리콘 분말은 이론적인 중량 증가율 66.7%의 실리콘 질화물로 전환되지만, 능동산화 반응에 의한 SiO(g) 증발로 인해 이론치보다 낮은 60% 내외의 값을 가진다.[9]
실리카의 탄소 열환원 방법(CRN)은 출발 원료(C, SiO2, N2)이 매우 저렴하고 풍부하기 때문에 비용적으로 가장 효율적인 질화규소 분말 제조 공정이다. 탄소 공급원이 존재하는 상태에서 SiO2의 CRN 공정은 일반적으로 1450∼1500℃의 온도 범위에서 진행되는데, CRN 공정에서 질화규소 분말의 특성을 결정하는 공정 변수는 C/SiO2 비율, CO/O2 분압, N2 유량, 공정 온도, 원료 SiO2의 입자 크기 및 비표면적, 불순물 등이 있다. CRN 방법의 반응성은 1450℃ 이하에서는 매우 낮아 제조가 어렵고, 온도가 1500℃까지 상승하면 원치않는 탄화규소(SiC)가 형성될 수 있어 까다롭다. 따라서 순수한 Si3N4 원료분말을 제조하기 위해서는 CRN 공정의 공정변수 최적화가 필수적이다.
SiO2 의 CRN 공정 과정에서 아래와 같은 두 가지 반응이 있을 수 있다.
CRN 공정에 사용될 수 있는 출발 원료는 규산염 기반 SiO2 혼합물, SiO2 겔, 석영 모래, 폐 실리카 흄, 규산염 및 붕규산염 유리 및 탄소 공급원(예: 활성탄, 카본 블랙, 카본 코크스 및 흑연 등)이 있다.
이미드 합성법은 고순도, 미세하고 균질한 크기 분포, 등축 형상을 가지는 질화규소 분말을 제조하기 위해 사용하는 화학적 합성 방법이다. 이미드 합성법은 상당한 양의 에너지를 소비하는 것으로 알려져 있다. 이 방법을 이용한 질화규소 분말의 합성은 다음의 두 단계 과정을 거친다.
초기에 사염화규소(SiCl4)를 저온(−50℃∼0℃)에서 액체 암모니아(NH3)와 반응을통해 중간 단계인 실리콘 다이이미드 고체 고분자가 생성된다.
또한, 상기 반응은 두 출발 물질 모두 액체 형태일 수도 있고, 한 가지 물질만 액체 상태일 수도 있고, 둘 다 기체 상태일 수도 있으며, 중간 단계 부산물인 NH4 Cl은 암모니아로 세척하거나 900℃의 불활성 분위기에서 열처리하여 제거할 수 있다. N2 분위기 하에서 1000℃ 온도에서 Si(NH) 2의 열분해 반응을 통해 비정질 Si3N4 분말을 얻을 수 있다.
이 비정질 질화규소 분말을 1300∼1700℃ 사이에서 열처리하면 결정질의 α 상 질화규소 분말을 얻을 수 있다.
이미드 합성법을 통해 생성된 α 상 질화규소 분말은 다른 두 가지 방법으로 생성된 분말보다 순도가 높은 반면, 공정 비용 및 공정의 복잡성, 유독물질인 액체 암모니아 처리등 안전 관련 문제 및 부산물 제거 난이도로 인해 접근성이 떨어지는 제조 방법으로 알려져 있다.[10]
연소 합성(CS) 또는 자기전파고온합성(SHS) 방법은 외부 점화제에 의해 시작되는 급격한 연소에 의한 반응을 유도하는 질화규소 분말 제조 방법이다. 이 공정은 질화물(Si3N4, AlN, TiN, BN, SiAlON 등), 탄화물(SiC, TiC, ZrC, Ti3 SiC2, Ti3 AlC2, Ti2 AlC2, Ti2 AlC 등), 붕화물(MgB2, TiB2, TiB2, ZrB2 등) 등 다양한 유형의 세라믹 분말을 제조하는 데 사용될 수 있다. 연소합성법은 에너지적으로 효율적이고 낮은 공정 비용, 높은 생산 수율, 단순한 장비 설계 등의 장점이 있다. 고압 N2 분위기에서 이루어지는 급격한 연소합성 공정으로 인한 발열 반응은 Si의 녹는점보다 온도를 더 상승시키고, 이로 인해 β-Si3N4가 주로 형성된다.
연소 합성법을 통한 질화규소 분말 합성에 사용되는 출발 물질은 Si, NaN3 및 NH4 Cl 등이 있다. 통상적으로 점화제로는 Ti 또는 Ti+C가 사용되며, 반응물 위에 Ti 분말을 위치시키고 텅스텐 코일을 이용하여 점화시켜 연소 공정을 개시하게 된다. 허나, 연소합성법에 의한 α-Si3N4의 제조는 연소 중 공정온도가 질화규소의 α-β 상변태 온도보다 더 높게 상승하기 때문에 어려운 것으로 여겨진다. 대신 α-Si3N4는 Fe계 첨가제와 함께 연소합성 반응에서 희석제로 사용될 수 있으며, 이는 최대 연소 공정온도를 낮춤으로써 질화규소의 분해 및 Si 의 용융을 방지하여, 질화규소 형성을 위한 충분한 핵생성 부위를 생성하고, N2의 확산을 증가시킬 수 있다. 연소 반응을 점화하고 유지하려면 최소 N2 압력이 필요한데, 압력 범위는 0.5 MPa에서 최대 100 MPa까지 보고된 바 있다.[11]
1.3 질화규소 세라믹의 소결 방법
고밀도 질화규소 소재 및 부품은 고온에서 소결하는 공정을 이용하여 제조할 수 있다. 소결 기술은 외부 압력을 사용하거나 액상소결을 위한 소결첨가제를 사용하거나, 또는 두 가지 방법을 동시에 사용하여 물질 확산 속도를 가속화시키는 방법이다. 질화규소 세라믹의 주요 소결 방법은 다음과 같이 세 가지로 분류할 수 있다.
-
• 반응 결합 질화규소
(Reaction-bonded silicon nitride, RBSN) -
• 상압 소결 질화규소
(Pressureless sintered silicon nitride) -
• 가스압 소결 질화규소
(Gas pressure sintered silicon nitride)
반응 결합 공정법은 Si 과 N2 간 반응을 이용하는 직접질화법의 하나로 질화규소 세라믹을 저비용으로 효율적이게 생산하는 방법으로, Si 분말을 원료로 질화규소 부품을 바로 생산하는 방법은 반응결합공정이 유일하다. 질화규소 세라믹은 1200-1600℃의 온도 범위에서 수 시간 동안 N2와 기상 반응하는 동안 in-situ 상으로 형성된다.[12] CIP(cold-isistatic pressing), 슬립 캐스팅(slip casting), 또는 사출 성형을 통해 Si 성형체를 만들고, 불활성 분위기에서 사전 소결 단계(1000℃ ∼ 1200℃)를 거쳐 적절한 강도를 얻은 후 N2 또는 N2-H2 또는 NH3 분위기 하에서 1200℃ ∼ 1450℃ 온도 범위에서 질화 공정을 진행한다.[13] Si 와 질화규소의 밀도 차이로 인해 RBSN이 생성되면 약 22%의 부피 팽창이 일어나나, 기존 성형체 내에 존재하는 기공 쪽으로 RBSN 이 형성되기 때문에 실질적인 치수 변화(± 0.1%)는 매우 작은 특징이 있다. 따라서, 이 RBSN 공정으로 생성된 질화규소는 복잡한 형태의 실형상 질화규소 세라믹 제품을 생산하는 데 사용될 수 있는 장점을 가진다. RBNS 공정의 단점은 공정 제어가 까다로운 측면이 있어서 미반응한 Si가 잔류할 수 있다는 것, 그리고 기공율이 약 20-30%로 RBSN의 기계적 특성과 내산화성에 치밀한 질화규소 대비 열악한 것이다. 이러한 물리적 특성을 향상시키기 위해 후소결(post-sintering)을 통해 완전히 치밀한 질화규소 세라믹을 얻기도 한다.
상압 소결 공정은 외부에서 추가적인 압력을 가하지 않고 세라믹을 소결하는 가장 매력적인 간단하고 경제적인 방법이다. 상압소결은 복잡한 모양의 밀도가 높은 세라믹을 생산하는 데 사용되며, 완전한 치밀화를 위해 물질 확산에 유리한 액상 소결용 첨가제를 사용하는 것이 일반적이다.[14]
소결에 앞서 액상 생성용 소결첨가제와 함께 α-Si3N4 원료분말을 볼 밀링 등과 같은 물리적 혼합방식을 통해 균질하게 혼합한 후 건식/습식 성형 공정을 통해 응용분야에 적합한 형태로 성형체를 만들어 주고, 이를 소결로를 이용하여 1500-1800℃의 온도 범위에서 소결해 준다. Meng 등은 BaO-Al2 O3-SiO2 유리와 함께 α-Si3N4 및 Si 분말을 첨가제로 사용하고, N2 분위기 하에서 1500℃ 에서 2시간 동안 상압소결을 실시하여, 98.8%의 상대 밀도를 갖는 조밀한 질화규소 소결체를 제조하는 것을 보고한 바 있다.[15] 최근 들어서는 높은 열전도도를 가지는 질화규소 세라믹의 상압소결 연구들 또한 활발하게 진행되고 있다.[16,17]
가스압 소결 공정 방법은 N2의 분압을 대기압 이상으로 증가시킴으로써 질화규소의 열분해를 억제하면서 벌크 밀도를 높일 수 있도록 하는 상압소결 공정법의 변형된 방식이라고 할 수 있다. 가스압 소결법을 사용하면 신뢰성이 높고 기계적/열적 특성이 우수한 질화규소 세라믹 소재를 경제적이로 짧은 소결 시간을 들여 대량 생산할 수 있다. 열간가압소결(Hot-press), 열간등방압소결(Hot-isostatic-press) 등의 가압 소결법에서 얻을 수 있는 이론 밀도에 가까운 질화규소 소결체를 가스압 소결법을 이용하여 효과적으로 얻기 위해 BN 분말 베드 및 2단계 소결법을 적용하는 등 다양한 소결 제어 공정이 수행된 바 있다. 또한, 가스압 소결법은 RBSN 질화규소를 완전히 치밀화 시키기 위해 후소결하는 공정으로 가장 적합하게 사용되는 방법이다.[18-20] Gola 등은 1950℃에서 3시간 동안 가스압 소결을 통해 Si 분말의 분쇄 밀링을 통해 고밀도/고열전도의 후소결된 RBSN을 개발한 바 있다. Li 등은 흑연 소결로에서 RBSN 공정을 거친 후 1900℃에서 12시간 가스압 소결 과정을 통해 β-Si3N4 입성장이 크고 격자 내 산소량을 낮게 만들어 열전도도 120 W/mK 을 달성하였다고 보고한 바 있다. (Fig. 2)
Fig. 2
흑연 분위기 활용에 따른 가스압소결된 반응결합질화규소(RBSN) 미세구조 내 b 상 입성장 차이 (a) 흑연 분위기 미활용 (저배율) (b) 흑연 분위기 활용 (저배율) (c) 흑연 분위기 미활용 (고배율) (d) 흑연 분위기 활용 (고배율) Adapted from Li et al. J. Eur. Ceram. Soc. 2017;37:4483-4490, with permission of the Elsevier and Copyright Clearance Center [20]
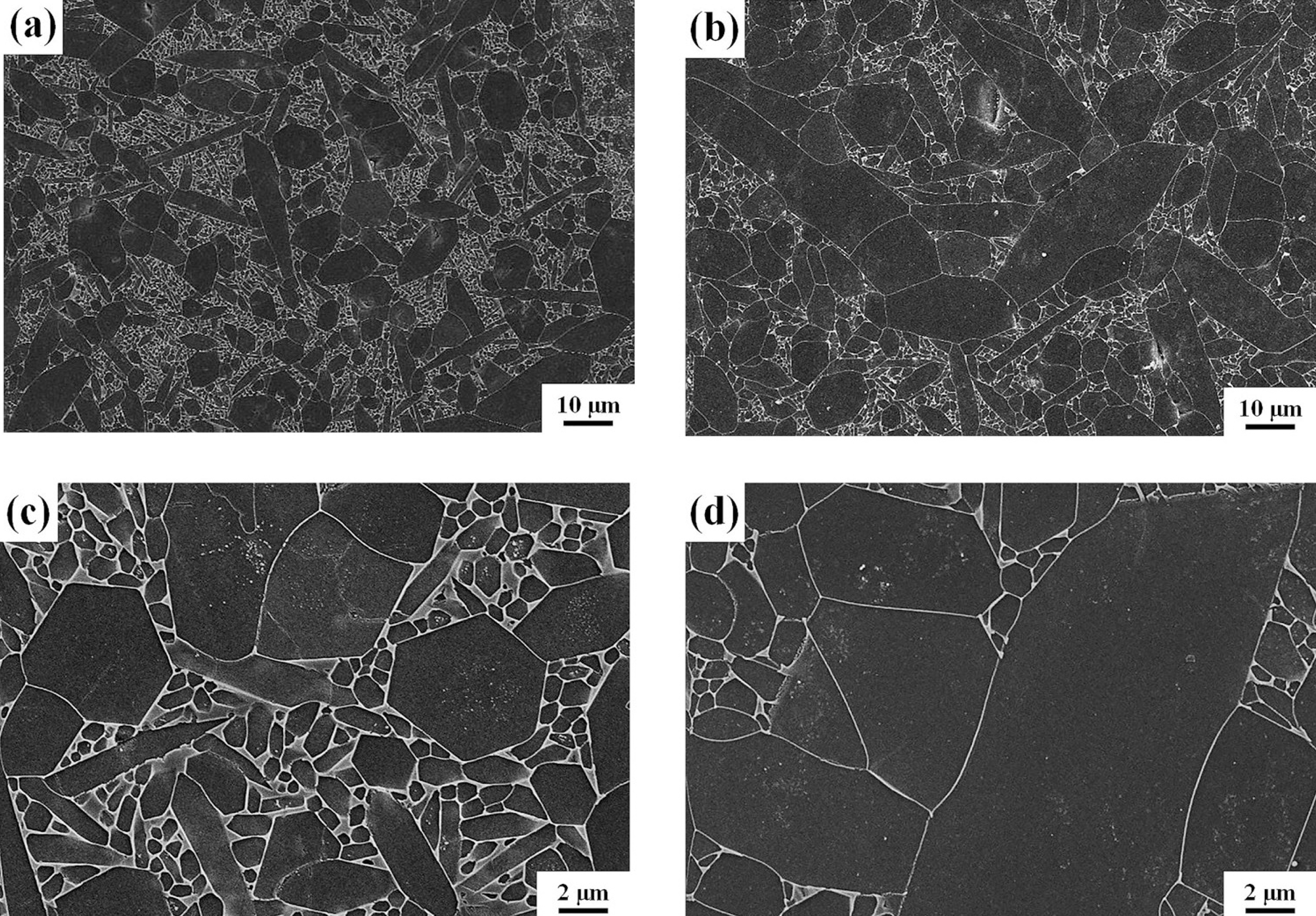
1.4 질화규소 세라믹의 응용 분야
질화규소 세라믹은 저밀도, 고내열충격성, 저열팽창계수, 내부식성 등의 고유한 특성으로 인해 전통적인 금속부품을 대체하여 구조, 자동차, 전자, 바이오메디컬 산업 등 다양한 분야에서 응용되고 있다. 우수한 내산화성 및 크리프 저항성, 낮은 유전 손실 등의 또 다른 특성들은 방위산업, 우주항공 분야 등의 응용 분야에도 사용이 가능하게 한다.
기계 및 자동차 산업에서 질화규소 세라믹 적용은 절삭 공구, 펌프 씰 부품, 세라믹 방탄소재, 롤러 및 베어링 볼, 가스 터빈 엔진 부품 또는 열 교환기, 터보차저 로터, 디젤 엔진 부품, 용융금속용 도가니, 열전대 피복 및 노즐 등 다양하게 사용되고 있다.
전자 산업에서 질화규소 세라믹은 전기차용 파워모듈에서 절연/방열기판 재료로 각광받고 있으며(Fig. 3), 전장 부품용 열 교환기 패널 및 납땜용 지그로도 사용되고 있다. 혹독한 환경에 노출되기 쉬운 항공 및 항공 우주 산업에서 질화규소 세라믹의 낮은 유전율과 유전 손실은 우수한 강도와 열충격 저항성과 결합되어 안테나 및 고속 미사일 레이더용 보호덮개로 적용될 수 있다. 최근 들어서는 질화규소의 생체적합성 소재 적용 연구가 활발하게 진행되고 있으며 척추 임플란트, 인공 고관절 및 무릎관절에 적용하거나 수술용 나사, 플레이트 및 스페이서를 만드는 데에도 사용되고 있다.[21]
본론: 질화규소 세라믹의 열전도 특성 및 기술 동향
질화규소 소재는 Si와 N 원자 간의 강한 공유 결합으로 이루어져 있기 때문에 열전도에 사용할 수 있는 자유 전자는 없는 것으로 여겨진다. 따라서, 질화규소 소재 내에서 열전도는 격자 진동에 의해서만 이루어지는 것으로 생각할 수 있다. 이러한 가정을 기반으로 Watari 등[22]은 Si3N4의 고유 열전도율을 추정하였으며, 상온에서 상한 열전도도를 약 400 W/m·K 로 보고한 바 있다. Hirosaki 등[23]은 분자 역학 계산을 사용하여 α 및 β-Si3N4의 열전도도를 계산하였는데, 결정구조 상 a축 및 c축 방향에서 α 및 β-Si3N4의 값은 각각 105, 225 및 170, 450 W/m·K 로 보고하였다.
실제 질화규소 세라믹의 열전도도는 열확산계수를 실험적으로 측정하고 아래의 식을 적용하여 계산 가능하다:
여기서, ρ는 밀도(g/cm3), Cp는 열용량(J/g·K), α(m2/s)는 측정된 세라믹 소재의 열확산계수이다. 열전도도는 고체의 밀도가 온도에 따른 변화가 미약하기 때문에 소재의 열확산계수가 주로 결정인자로 여겨진다. 열확산계수는 평균 포논 속도와 총 평균 자유 경로에 따라 달라집니다. 포논 속도는 온도에 따라 달라지는 반면, 총 평균 자유 경로는 물질 고유의 격자 특성과 제조된 재료 내에 존재하는 결함 및 결정 입계에 따라 영향을 받으며, 이는 질화규소 세라믹에도 유효하다. 실험적으로 제조된 질화규소 세라믹의 가장 높은 열전도도는 Zhou 등이 보고한 177 W/m·K으로 알려져 있다.[24]
벌크 세라믹 소재를 만들기 위해서는 제조하고자 하는 물질과 필요한 경우 소결 첨가제를 이용하여 고상 소결 또는 액상 소결에 의해 만들 수 있다. 질화규소 세라믹의 경우, 구성 원자 간 강한 공유 결합으로 인해 물질 확산이 매우 어렵기 때문에 고상 소결법으로는 치밀한 세라믹을 얻지 못하고 물질 확산을 도와주는 소결 첨가제를 혼합하여 액상 소결로 치밀체 질화규소 세라믹을 얻는 것이 일반적이다.
일반적으로 소결 과정에서 공융 액상을 얻기 위해 적어도 두 종류의 소재(주 성분 + 소결 첨가제)의 혼합물을 출발 원료로 사용한다. 소결 첨가제는 주 성분과 반응하여 소결 과정에서 일정 온도가 초과하면 공융 액상을 생성한다.[25] 액상 소결을 효율적으로 하기 위해서 필요한 몇 가지 사항은 낮은 접촉각, 낮은 이면각, 허용 가능한 액체 부피 비율, 액체에 대한 높은 고체 용해도, 입자 고체의 균일한 패킹, 액상의 균일한 분포 및 입자 크기이다. 액상 소결이 완료된 후 냉각 과정에서 액상은 응고되어 고상으로 전환되는데 질화규소의 경우 액상의 조성 및 열처리/소결 조건 따라 비정질 유리상 또는 산질화물계 결정상으로 남게 된다. 비정질 유리상의 경우 열전도도가 약 1 W/m·K 내외에 불과하므로 소결된 질화규소 세라믹의 전체 열전도도를 저하시키는데 결정적인 역할을 한다.[26] 일반적으로 질화규소 세라믹의 높은 열전도도를 얻기 위한 전략 중 하나로 비정질 유리상의 함량을 낮추는 것이 유리하나, 벌크 질화규소 세라믹의 소결 후 밀도를 높이기 위해서는 일정량 이상의 액상이 필요하므로 적절한 액상량의 조절이 필요하다. 질화규소 세라믹 소결체를 얻기 위해서는 액상 소결에 적합한 첨가제를 선택하는 것 또한 중요하다. 일반적으로 질화규소와 소결 첨가제 간 공융 액상 형성 온도가 낮은 첨가제를 사용하는 것이 바람직하지만 질화규소 세라믹을 고온 환경에서 사용할 경우라면 공융 온도가 너무 낮아도 곤란할 수 있다.
2.1 출발 원료분말의 영향
출발 원료분말의 역할은 벌크 질화규소 세라믹 소결체의 기계적/열적 특성을 결정하는 데 중요하다. 원료 분말의 평균 입자 크기 및 분포, 순도, 비표면적 등은 소결체 밀도 및 미세구조에 영향을 미치는 것으로 알려져 있으므로 출발 원료분말을 선택할 때는 매우 주의해야 한다. 반응 결합 질화규소(RBSN)의 경우, 출발 원료는 소결 첨가제를 포함하는 Si 분말이 주로 사용되며, Si 분말 특성이 질화규소의 특성 및 미세 구조에 미치는 영향에 대한 많은 연구가 있어 왔다.
Si 분말의 입자 크기 분포 또는 불순물 함량(Fe, Al, O 등)은 질화규소 소결체의 최종 밀도, 미세 구조, 열전도도에 중요한 역할을 하는 것으로 보고되어 왔다. Hirao 등[27]은 RBSN 공정을 사용하여 소결된 질화규소의 미세 구조와 열전도도에 대한 Si 입자 크기의 영향을 보고하였다. 저자들은 RBSN 공정을 이용한 질화규소 세라믹 개발을 위해 두 가지 크기(S1, D50 = 0.7 µ m / S2, D50 = 7 µ m)의 Si 분말을 원료로 하고 1400℃에서 8시간 동안 질화 및 1900°C에서 12시간 동안 후소결한 결과 미세 구조는 두 경우 모두에서 현저한 Bi-modal 분포를 나타냈는데, 입자가 미세한 S1은 S2보다 Bi-modal 분포가 더 뚜렷하였다. 열전도도의 경우 S2(121 W/mㆍ K)는 S1(112 W/mㆍ K)에 비해 약간 높았는데, 미세한 입자보다 조대한 Si 입자로부터 제조된 질화규소 세라믹의 열전도도가 높은 것은 산소 불순물의 함량이 낮기 때문이다. 이 연구는 Si 입자가 클수록 산소 함량이 낮아 미세한 Si 입자보다 열전도도가 우수하다는 것을 보여준다. 또 다른 연구[28]의 경우 또한 RBSN 방법을 사용하여 질화규소 세라믹을 제조할 떄 Si 입자의 크기가 소결밀도에 미치는 영향을 보고한 바 있는데, 조대한 Si 분말이 미세한 Si 분말보다 더 많은 금속 불순물을 함유하고 있다는 것 또한 비교하였다. 조대한 Si 분말로 제조된 질화규소는 상대 밀도(91.9%)와 열전도도(84 W/mㆍ K)가 미세 분말을 사용하여 개발된 것(각각 99.9%, 121 W/mㆍ K) 대비 현저하게 낮았는데, 상대 밀도 및 불순물 함량과 같은 다른 인자가 동일한 수준이 아니면 원료 Si 분말 입자 크기와 열전도도 사이에 직접적인 상관관계를 만들 수 없다는 것을 보고한 것이다. Gola 등[19]은 다양한 온도에서 소결된 RBSN 질화규소의 열전도도에 대한 조대한 Si(4.60 µ m)와 분쇄된 미세한 Si 분말(0.43 µ m)의 영향을 보고한 바 있다. 볼밀링을 통해 미세화 시킨 Si 분말의 산소 함량이 조대한 Si 분말의 0.91 wt%에서 2.27 wt%로 증가하였으며, 증가한 산소량에 의해 최종 소결체의 입계상 량과 두께를 증가시켰기 때문에 조대한 Si 분말을 사용한 RBSN 질화규소 소결체의 열전도도가 더 높은 결과(미세 Si: 51.94 W/mK, 조대 Si: 89.61 W/mK)를 나타내었다. 또 다른 연구에서도 Go 등[29]은 0, 1, 2, 4 및 12 시간 볼 밀링된 Si 분말을 사용하여 밀링 시간이 RBSN 질화규소의 특성에 미치는 영향을 보고하였다. 0, 1, 2, 4 및 12 시간 밀링된 Si 분말의 산소 함유량은 각각 0.54, 1.18, 1.32, 1.60, 2.57 wt%로 밀링 시간에 따라 증가하였는데, 질화규소 소결체의 열전도도 값은 0∼4 시간 밀링 조건까지는 크게 변화하지 않다가, 12시간 밀링 조건의 경우 질화규소 소결체 열전도도에 급격한 감소가 나타났다. 이는 12시간 밀링 조건에서 입계의 두께가 크게 증가함에 따라 β-Si3N4 결정 입자 간 연결성을 떨어뜨린 것으로 보고하였다. 이는 TEM 분석을 통해 확인되었는데, 12시간 동안 입계의 두께가 4시간 밀링 조건(0.9 nm)의 두 배인 1.8 nm로 증가하는 것이 확인되며 이러한 입계 두께 증가로 인한 열저항이 커지는 것으로 결론지었다. (Fig. 3)
한편, Oh 등[30] 또한 다양한 입도 분포의 Si 분말을 사용하여 RBSN 질화규소 세라믹을 제조함에 있어 모든 샘플에 대해 평균 입도 크기는 ∼1 μm로 유지하는 동시에 입도 분포만 다르게 했을 때 질화규소 특성에 미치는 영향을 보고하였다. 반도체용 고순도 Si 잉곳 스크랩으로부터 제조된 Si 분말과 Y2 O3-MgO 첨가제를 혼합하여 RBSN 질화규소를 제조하였는데, Si 분말의 입도 분포(WPSD) 폭이 증가함에 따라 열전도도가 감소하는 경향을 보고하였다. WPSD가 증가함에 따라 미세한 분말의 비율이 높아지고 그에 따라 전체 산소 함유량이 상승하는 것으로 확인되었으며, 그에 따라 WPSD가 좁은 경우 산소 함량이 낮아져 81 W/mK 열전도도를 나타낸 반면 WPSD가 넓어진 경우 67 W/mㆍ K의 낮은 열전도도를 나타내었다. 단, 기계적 특성에 있어서 강도값은 미세한 기지상을 형성시킬 수 있는 미세한 출발 원료 입자 비율이 높게 함유된 WPSD가 넓은 경우에 높은 값을 나타내었고(1.02 GPa) 그에 비해 파괴 인성 값에는 큰 영향이 없는 것으로 보고되었다.
출발 원료의 주 성분인 Si 분말만이 아니라 소량이 함유됨에도 불구하고 소결 첨가제의 특징이 RBSN 질화규소 소결체의 열전도 특성에 영향을 미칠 수 있는 것으로 알려져 있다. 소결 첨가제가 미세 입자를 갖는 것은 액상의 균일한 분포에 도움이 되는 반면, 조대한 소결 첨가제의 경우 액상의 불균일한 분포를 형성할 수 있을 것으로 생각되는데, Go 등[31]이 조대한 입자로 구성된 소결 첨가제가 액상의 불균일한 분포를 야기하여 국지적인 입성장을 유도함으로써 열전도도를 개선할 수 있다는 것을 발견하였다. 미세한 (1.6 µ m) MgO 및 조대한(5.9 µ m) MgO 분말을 각각 RBSN 질화규소 소결에 적용하였을 때 열전도도의 경우 미세함 MgO 경우(77.3 W/mㆍ K) 대비 조대한 MgO 경우(87.8 W/mㆍ K)가 더 높은 값을 나타내었다. 미세한 MgO 입자의 균일한 분산은 액상을 균일하게 형성시킴으로써 질화규소의 비정상 입성장을 방해한 반면, 조대한 MgO 입자로 인한 액상의 불균일한 분산은 국지적인 비정상 입성장 숫자를 늘리는 것으로 나타났다. (Fig. 4)
2.2. 소결 첨가제의 영향
질화규소 소재의 Si-N 사이의 강한 공유 결합성은 원자 단위의 확산을 극히 어렵게 만들기 때문에 고상 소결에 의한 치밀화가 곤란한 특징을 가지게 한다. 따라서, 산업적으로 활용할 수 있는 수준의 적당한 온도에서 치밀한 질화규소 세라믹을 얻기 위해서는 액상 소결을 유도할 수 있는 소결 첨가제가 일반적으로 사용되며, 이 첨가제는 질화규소 및 질화규소 표면에 상존하는 SiO2와 공융 액상을 형성시킴으로써 액상 소결 과정을 촉진시킨다. 소결 첨가제는 질화규소의 밀도를 높이는 데 도움이 될 뿐만 아니라, 기계적/열적 특성에 중요한 영향을 미치는 소결체의 미세 구조 및 2차상 구성을 결정하는 데 중요한 역할을 한다. 또한, 소결 첨가제가 촉진하는 액상 소결에서 일어나는 질화규소 결정의 용해-재석출 과정을 통한 입성장 진행을 통해 질화규소 결정 내에 격자 산소가 제거됨으로써 열전도도를 높일 수 있다. 현재까지 Y2 O3, MgO, Al2 O3 등과 대표적인 산화물을 포함하여 질화규소 세라믹의 밀도를 높이기 위해 다양한 소결 첨가제가 사용되고 있다. 소결 첨가제의 분류는 산화물(Y2 O3, MgO, Al2 O3, ZrO2 등) 및 비산화물 첨가제(Mg3 N2, Be3 N2, ZrN, ZrC 등) 또는 이들의 혼합물로 이루어는데, 각 유형의 첨가제는 공융 액상의 점도, 화학적 조성, 공융 온도, 냉각 후 2차상 형태(결정질/비정질) 등이 상이한 특징을 가지고 있으므로 소결 첨가제가 실리콘 질화물의 최종 특성에 미치는 영향은 무시할 수 없을 정도로 큰 것으로 알려져 있다.
질화규소와 고용체를 형성하지 않는 산화물 첨가제들이 일반적으로 질화규소 시스템에서 높은 열전도도 달성을 위해 널리 사용되고 있다. Okamoto 등은[32] Y2 O3-Nd2 O3-MgO 또는 Al2 O3를 소결제로 사용하여 RBSN 공정으로 질화규소 세라믹 소결을 수행하였는데, 특히 MgO와 Al2 O3가 열전도도에 미치는 영향에 집중하였다. MgO 또는 Al2 O3 첨가량이 1 mol% 로 낮은 경우 RBSN 질화규소 세라믹의 상대 밀도는 Y2 O3-Nd2 O3-Al2 O3 경우가 Y2 O3-Nd2 O3-MgO 경우보다 높은 것으로 확인되었으며, 2 mol% 이상에서는 거의 유사한 것으로 나타났다. 그러나, 첨가량과 무관하게 질화규소의 열전도도는 Y2 O3-Nd2 O3-MgO 경우가 Y2 O3-Nd2 O3-Al2 O3 경우보다 훨씬 높게 나타났는데, 2 mol% MgO 첨가로 최대 열전도도는 128 W/mㆍ K를 달성한 반면, Al2 O3의 경우 가장 높은 열전도도가 70 W/mㆍ K에 불과할 정도로 큰 차이를 보였다. MgO 또는 Al2 O3 가 첨가되지 않은 Si3N4-Y2 O3-Nd2 O3 소결체의 열전도도가 98W/m·K 인 것을 감안할 때 Al2 O3의 첨가로 인해 질화규소 세라믹의 열전도도가 급격하게 낮아지는 것으로 보고하였다. 이는 Al2 O3 의 첨가로 인해 Si3N4에서 Si 및 N 원자 자리를 Al 및 O 가 치환하면서 SiAlON 상이 형성되기 때문으로, SiAlON 상은 Si3N4 대비 격자 구조를 왜곡하고 산소 공공을 만듦으로써 포논 산란이 강화되어 감소하는 것으로 인정되고 있다.(Fig. 5)[26] 따라서, Al2 O3 첨가제는 높은 열전도도를 갖는 질화규소 세라믹을 얻기에는 바람직하지 않은 첨가제라는 것을 추론할 수 있다.
Fig. 5
주사전자현미경으로 관찰된 MgO 소결 첨가제 크기에 따른 후소결 반응결합질화규소(RBNS)의 미세구조 차이 (a) 조대한 MgO (b) 미세한 MgO (c) (a)의 이미지 분석 결과 (d) (b)의 이미지 분석 결과 [31]
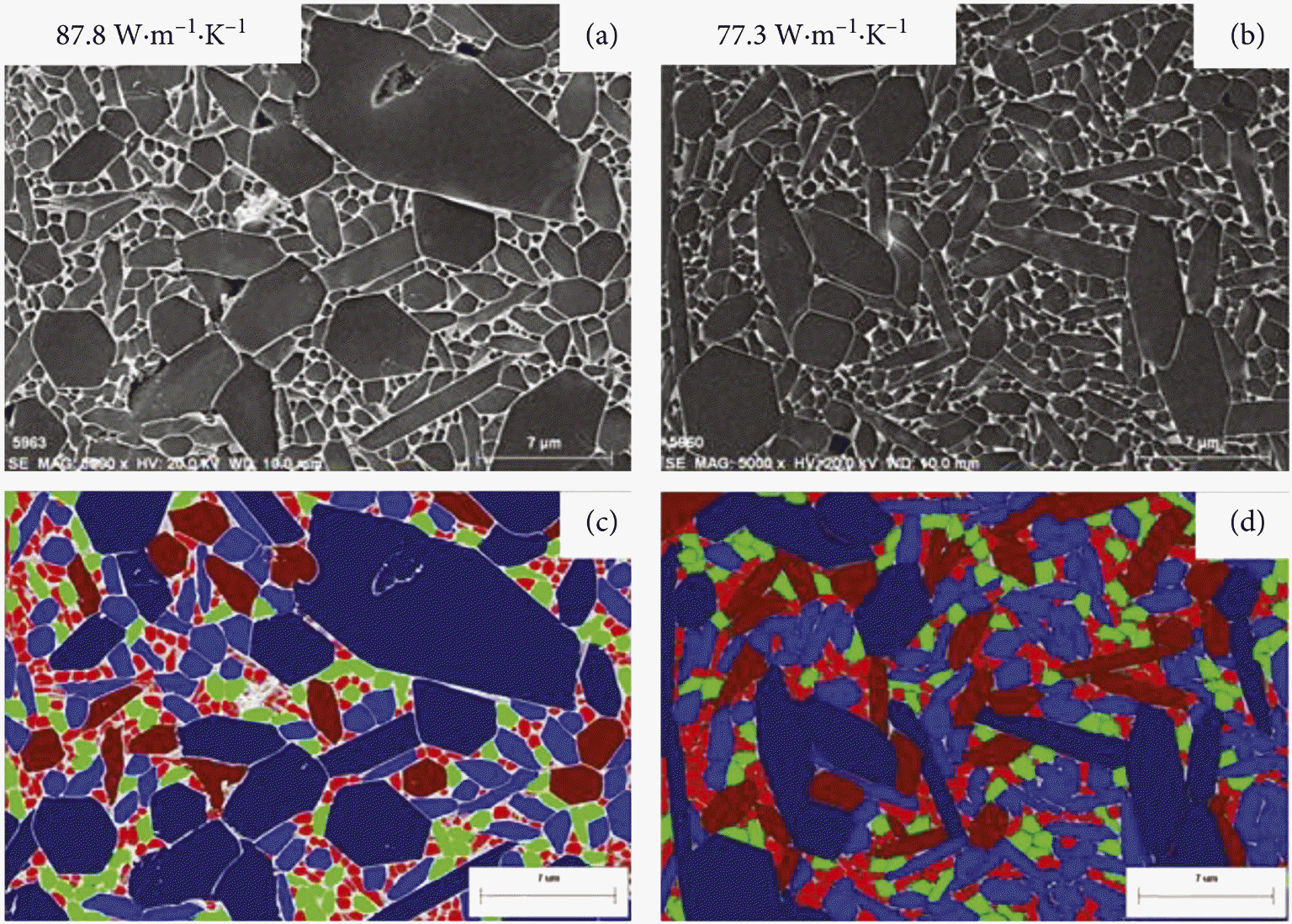
Zhu 등은[33]는 RBSN 공정으로 소결된 질화규소 세라믹의 열전도도을 연구하기 위해 소결 첨가제 조합 2가지, Y2 O3–MgO(YM)와 Yb2 O3–MgO(YbM)에 대해 보고하였다. 1350°C에서 8시간 동안 질화 후 1900°C(N2 압력 1 MPa 하)에서 후소결한 질화규소 세라믹의 경우 YM의 경우 상대 밀도(100%)가 YbM(93%) 대비 7% 가량 높았음에도 불구하고, 열전도도의 경우 YM(76 W/mㆍ K) 시편이 YbM(83 W/mㆍ K) 시편보다 낮았는데, YbM 샘플의 열전도율이 더 높은 이유을 2차상 양과 상대적으로 큰 결정립을 가지기 때문으로 설명하였다. Kitayama 등[34]은 질화규소 세라믹 소결 시 격자 내 산소를 제거하는 데에 Y2 O3보다 Yb2 O3의 우수하다고 보고한 바 있는데, 질화규소 소재에서 격자 내 산소의 존재는 열전도도를 감소시킨다는 것이 널리 받아들여지고 있다.[26] Kusano 등[35]의 연구에 따르면, 소결 첨가제 MgO를 MgSiN2로 대체할 때 열전도도가 증가했다고 보고한 바 있다. 소결조제로서 Y2 O3-MgO 또는 Y2 O3-MgSiN2를 사용한 질화규소 소결체를 RBSN 공정을 거쳐 제조한 결과, Y2 O3-MgO 소결 첨가제를 사용한 질화규소 세라믹의 열전도도는 89 W/mㆍ K인 반면, 첨가제로 Y2 O3-MgSiN2를 사용한 경우 열전도도 값이 101 W/mㆍ K로 향상되었다. 이는 MgO를 MgSiN2로 대체하면 열저항의 원인이 되는 2차상 및 격자 내 산소의 양이 감소한 것이 질화규소 세라믹 열전도도 증가의 가능한 원인으로 보고하였다.
RBSN 공정으로 제조된 질화규소 세라믹의 첨가제 조합 함량에 따른 열전도도 영향에 대한 체계적인 연구는 Zhou 등[36]에 의해 수행되었다. 가장 널리 사용되는 소결 첨가제 조합인 Y2 O3–MgO을 사용하되, Y2 O3 함량을 0-5 mol% 범위, MgO 함량을 0-8 mol% 범위로 비율을 다양하게 조정하여 질화규소 열전도도에 미치는 영향을 연구하였다. MgO 또는 Y2 O3 중 어느 하나가 배제된 조합에서 질화규소 소결체는 매우 긴 시간(24시간) 동안 소결해도 완전하게 치밀화되지 않았으므로, 양호한 상대 밀도(즉, 95% 이상)를 얻기 위해서는 두 산화물 첨가제를 모두 사용하여야 한다고 보고하였다. 또한, 일정량을 초과하는 MgO 첨가량의 증가는 열전도도에 아무런 차이를 주지 못한 반면 Y2 O3 첨가량의 증가에 따라 질화규소의 열전도도가 증가한다는 것이 상세 연구를 통해 추가로 확인되었다. 따라서, 해당 소결 첨가제 조합에서 MgO의 역할은 공융 액상 형성 온도를 낮추어 치밀화 촉진에만 유용한 반면 Y2 O3의 역할은 또한 질화규소 결정입자 내 산소를 제거하는데 영향을 미쳐 벌크 세라믹의 열전도도를 향상시키는 데 기여한다는 것을 보고하였다.
2.3 질화규소 세라믹에 함유된 불순물의 영향
Si 분말을 이용하는 RBSN 공정 경로가 질화규소 분말을 이용하는 일반적인 가스압 소결보다 유리한 장점 중 하나는 Si 원료의 불순물 함량이 질화규소 원료 내 불순물에 비해 적기 때문이다. RBSN 질화규소의 제조에 사용되는 Si 원료 분말은 크게 두 범주의 순도를 가지는데, 하나는 고순도 반도체 등급의 Si 분말이고 다른 하나는 저순도의 일반산업 등급 Si 분말이다. 많은 논문 연구들에서는 고순도 Si 분말을 사용하여 RBSN 질화규소의 제조 및 특성을 보고하는 것이 일반적이지만, 산업에 실용적인 적용을 위해서는 다양한 금속 불순물을 함유한 일반 Si 분말의 사용이 우선적으로 고려되어야 하는 부분이 있다. 따라서, 어떤 연구들은 Si 분말에 함유된 불순물이 RBSN 질화규소의 특성에 미치는 장단점을 보고한 바 있다. 이러한 금속 불순물은 가끔 질화 반응 및 소결 치밀화도를 향상시키기 위해 촉매로서 출발 원료 분말에 의도적으로 첨가되기도 하는데, 이러한 연구에서 대부분의 금속 불순물이 β 상 형성을 촉진하면서 α 상 형성을 저하시킨다는 것이 확인된 바 있다.
금속 불순물 또는 첨가제가 RBSN에 미치는 영향을 다양하게 연구된 바 있다. Pavarajarn 등은 다양한 금속 원소(Lu, Mg, Ca, Ce, Y, Yb, Ag, Cu, W, Fe 및 Cr)가 Si의 질화 반응에 미치는 영향을 보고하였는데,[37] RBSN의 미세 구조, 상변태 및 특성에 대한 다양한 요소의 역할이 평가되었다. 금속 불순물이 형성시킬 수 있는 소량의 액상의 존재 뿐만 아니라 금속 불순물의 전자기적 특성이 β 상 형성을 촉진하는 역할을 한다고 보고한 바 있다. Mitomo[38]는 제어된 PO2 압력 하에서 Fe와 Al이 Si의 질화에 미치는 영향을 연구한 바 있다. 두 불순물 모두 Si의 질화를 가속화했지만, Fe 첨가는 α 형성을 촉진하는 반면, Al은 β 상 형성을 촉진시킨다고 보고하였다. 마찬가지로, Mukerji 등[39]은 Ti 및 Hf 불순물이 있을 때 RBSN 질화규소 내 β 상 비율이 증가하는데 해당 불순물 원소가 질소 운반체로 작용함으로써 β 상 형성을 위한 활성화 에너지를 감소시킨다고 보고한 바 있다.
Kusano 등[35,40]은 RBSN 질화규소 세라믹의 기계적/열적 특성에 대한 Fe와 Al 불순물의 영향에 대해 체계적인 연구를 수행하였는데, 일련의 연구에서 Fe를 0, 0.1, 1, 5 wt% 첨가 시 질화규소 세라믹의 열전도도는 각각 82, 81, 80, 53 W/mK로 나타난 반면, Al 불순물을 0, 0.01, 0.1, 0.2, 0.4 wt% 첨가한 경우 질화규소의 열전도도가 91.9, 83.7, 74.1, 66.2, 58.0 W/mK로 급격하게 저하되는 현상을 보고한 바 있다. Fe는 1 wt% 첨가해도 열전도도가 거의 감소하지 않은 반면, Al은 0.01 wt%만 첨가하더라도 열전도도가 약 10% 가량 저하될 정도로 Al이 열전도도에 미치는 영향이 현저한 것이었다. 한편, Fe와 Al이 첨가된 질화규소 소결체의 굽힘 강도는 두 불순물 간에 큰 차이를 보이지 않았으나, 질화규소의 파괴 인성은 Fe 및 Al 첨가에 따라 감소하는 양상을 나타내었다. 따라서, 질화규소 소결체에서 목표하는 특성을 얻기 위해서는 개선하고자 하는 특성을 염두에 두고 필요한 원료의 품질(불순물, 입자 크기 등)을 잘 선택해야 한다.
2.4 미세구조의 영향
열전도도 계산식에 의하면 어떤 소재의 열전도도는 밀도의 상승에 따라 증가할 수 있다. 세라믹의 치밀화는 미세구조의 형성에 따라 달라질 수 있기 때문에, 미세구조는 질화규소 세라믹의 열전도도를 결정하는 데 결정적인 역할을 한다.
고온에서 소결된 질화규소 세라믹 미세구조는 β-Si3N4 입자로 구성되는데, 이 입자의장경비가 길수록 열전도도 개선 현상이 나타나는 연구들이 보고되어 왔으며 이러한 현상을 설명하고자 하는 연구들이 지속적으로 수행되어 왔다. 특히, Kitayama 등[41]은 질화규소 세라믹의 열전도도에 대한 다양한 미세 구조 요인의 역할을 연구했는데, Effective medium 이론에 따라 계산을 했을 때 결정입계의 두께 변화가 1∼10 nm 범위 에서 변화할 때 열전도도가 큰 폭으로 변화한다고 보고하였다. 질화규소 세라믹의 결정입계는 비정질 유리상으로 구성되어 있고, Si-Me-O-N 계 비정질 유리상의 열전도도는 약 1W/mㆍ K인 것으로 알려져 있기 때문에, 질화규소 세라믹 내에서 비정질 유리상의 구성 비율이 높아질수록 전체 벌크 세라믹의 열전도도가 분명히 감소된다. 비정질 유리상과는 다르게 질화규소 입자 크기 증가는 열전도도를 크게 증가시킬 수 있는 것으로 계산되는데, 1 µ m에서 9 µ m로 질화규소 구성 입자 크기를 증가시키면 열전도도가 55 W/mK에서 110 W/mㆍ K로 증가하는 것으로 보고되었다.
Hirao 등[42]은 질화규소 세라믹 내에서 이방성 미세구조가 열전도도에 미치는 영향을 보고한 바 있는데, 미세구조 이미지에서 큰 입자의 면적비가 증가하면서 열전도도가 크게 향상되었다고 언급하였다. 질화규소 세라믹의 열전도도는 큰 입자의 면적비가 20%일 때는 80 W/mㆍ K에 불과하였으나 큰 입자의 면적비가 60%일 때는 120 W/mㆍ K로 1.5배 증가함을 보고하였다. 또한, 질화규소 β 상 입자의 정렬 방향성이 열전도도에 상당한 영향을 미친다는 것도 보고하였는데, β 상 입자의 c축 방향으로 정렬된 면의 열전도도는 항상 β 상 입자의 c축 방향 수직으로 정렬된 면의 열전도도보다 높게 나타났다. 즉, β 상 입자의 c축 방향과 평행하면 열 전달이 촉진되고 수직인 방향으로 이동할 때는 열 전달이 억제된다고 할 수 있다.
결론
최근 들어 본격적으로 보급되고 있는 전기자동차의 전기적 구동을 책임지는 전력반도체 파워모듈의 집적화·고밀도화 추세로 인해 발열 문제가 심화될 것으로 예측됨에 따라, 발열로 인한 고장 또는 수명 저하에 대비한 고신뢰성 소재 및 대면적 방열기판 제조공정 기술의 확보가 반드시 필요해 지고 있으며, 혹한/혹서 등 환경의 변화에도 신뢰성을 유지하기 위한 기술적 장애물들이 이슈화 되고 있다.
방열기판 소재로 각광받는 질화규소 세라믹 소재에 있어 사용자 요구에 맞는 균형이 요구되고 있다. 우수한 방열 성능 구현을 위해서는 질화규소 기판 두께의 감소, 금속접합 두께의 증가, 질화규소 소재의 열전도도 향상 등이 필요한데, 특히 열전도도가 향상되면 기계적 특성이 동시에 변화하기 때문에 질화규소 세라믹의 장점이 손실될 우려가 있으므로, 열전도-강도 간의 상보적인 관계를 넘어서는 기술적 진보라는 숙제가 여전히 남아있다.
본문에서 질화규소 세라믹의 열전도도를 높이기 위한 다양한 기술적 고려사항에 대해 기술하며, 세부적인 사례와 함께 기술적인 진보 방향에 대해 서술하였다. 열전도도 향상을 위해서는 원료 분말에 불순물의 유입을 최소화하면서, 액상 소결에 필요한 소결 첨가제의 적절한 선택, 그리고 가스압 소결 공정에 의한 비정질 유리상 최소화 및 입성장 제어를 통한 미세구조 최적화가 필요하다.
연구개발 측면에서는 많은 기술적인 진보가 있어왔음에도 불구하고, 양산되고 있는 질화규소 기판의 열전도도는 90 W/mㆍ K 이하로 높지 않기 때문에 오랜 연구를 통해 밝혀진 다양한 열전도도 결정인자들을 제어할 수 있도록 실질적인 제조 기술로 확장하는 것이 향후에는 더욱 요구될 것으로 사료된다.