서론
1.1 열전 현상 및 열전 소재
열전(thermoelectric) 현상은 반도체 특성을 갖는 소재에서 열에 의해 캐리어(carrier)가 이동함에 의해 발생하는 열에너지와 전기에너지의 직접적이고 가역적인 변환 현상으로, 이를 이용하면 온도를 측정하거나, 전기인가에 의해 물체를 냉각/가열하거나, 온도차를 유발하여 전기를 생산할 수 있다.[1,2] Fig. 1에 p형 반도체 특성의 열전소재와 n형 반도체 특성의 열전소재를 전극을 이용하여 직렬로 연결한 구조의 열전모듈(thermoelectric module)을 나타내었으며, Fig. 1.a 는 펠티어(Peltier) 효과에 의한 열전냉각/가열(thermoelectric cooling/heating), Fig. 1. b는 제벡(Seebeck) 효과에 의한 열전발전(thermoelectric power generation)의 구동 원리를 도식화 하였다.
열전모듈은 일반적으로 절연기판-전극-열전소재-전극-절연기판의 대칭적이고 간단한 구조로 구성되기 때문에 열전냉각 및 열전발전은 시스템의 효율이 열전소재의 성능과 직결되는 소재 의존성이 큰 기술이다. 열전소재의 성능은 열에너지와 전기에너지의 변환 효율을 의미하며, 다음 Equation (1)로 정의되는 무차원 성능지수(dimensionless figure of merit) zT로 나타낸다.[3]
Equation (1)에서 σ, S, κ total은 각각 열전소재가 사용되는 절대온도 T에서 전기전도도(electrical conductivity), 제벡계수(Seebeck coefficient), 열전도도(thermal conductivity)이며, 분자의 σS2을 파워팩터(power factor)라 한다. 적용온도에 따라 zT가 높은 소재가 각각 개발되고 있으며, Bismuth-Telluride (Bi-Te)계(250°C 이하), Pb-Te계(200–500°C), Skutterudite계 (300–600°C), Si-Ge계(500–1000°C) 등이 1.0 이상의 높은 zT를 나타내는 대표적인 열전소재이다.[4] 최근의 소재 연구는 이들 열전소재의 성능 증대를 중심으로 진행되고 있으며, Equation (1)로부터 파워팩터 증대 또는 열전도도 저감을 통하여 성능 증대가 가능함을 알 수 있다. 그러나 Fig. 2에 나타낸 바와 같이 높은 전기전도도와 높은 제벡계수 간의 상쇄 관계(전하밀도가 증가하면 전기전도도는 증가하지만 제벡계수는 감소) 및 높은 전기전도도와 낮은 열전도도 간의 상쇄 관계(열전도도는 전자열전도도와 격자열전도도를 포함하며, 전자열전도도는 전기전도도에 비례)라는 물리적 제한이 있어 실질적인 zT 증대를 구현하기 위해서는 두 가지 상쇄 관계를 극복할 수 있는 전략이 필요하다.
1.2 Bi-Te계 열전 소재
Bi-Te계 열전소재는 0.1–0.2 eV의 좁은 band gap 을 가지는 반도체 특성의 소재이며, Fig. 3에나타낸 바와 같이 ab-plane에서 Bi/Sb와 Te/Se가 강한 공유 및 이온결합을 형성하고 있어 전기전도 특성인 전기전도도와 제벡계수가 높을 수 있는 소재적 인자를 포함하고 있음과 동시에 c축 방향으로 결합력이 약한 van der Waals 결합을 형성하여 열전도도가 낮을 수 있는 인자도 가지고 있는 이상적인 구조의 소재이다.[5] 상용소재의 조성은 p형 소재의 경우 Bi 자리에 Sb를 첨가한 Bi0.5 Sb1.5 Te3, n형 소재의 경우 Te 자리에 Se를 첨가한 Bi2 Te2.7 Se0.3에 소량의 이종원소를 첨가한 조성이 주로 사용된다.[6]
Bi-Te계 상용소재는 주로 zone melting 공정을 이용한 ingot 형태로 제조되고 있다. 이는 높은 파워팩터를 구현할 수 있는 즉, 상대적으로 낮은 전하밀도에서 높은 제벡계수를 구현하고 동시에 높은 전기전도도를 얻기 위해 결정배향성이 큰 ingot 형태로 제조하여 높은 이동도의 소재를 제조하는 것이 필요하기 때문이다. 하지만 결합력이 약한 van der Waals 결합 또한 정렬되기 때문에 기계적 신뢰성이 낮은 단점이 있다. Bi-Te계 열전소재의 응용확대를 위해서는 성능 증대는 물론 기계적 신뢰성 향상, 가격 경쟁력 확보 등이 필수적이기 때문에 기존 zone melting 공정의 장점을 유지하면서 단점을 극복하기 위한 소재 개발 및 제조 공정 개발이 진행되고 있다. 본 논문에서는 Bi-Te계 열전소재를 제조하는 공정기술과 특징에 대해 기술하고 최근 확립된 유사정형압출(near net shape hot extrusion) 기술에 대해 소개하고자 한다.
본론
2.1 Zone melting에 의한 ingot형 소재 제조 공정
Zone melting 공정에 의한 ingot 제조는 (1) 조성비에 따른 원료금속의 준비, (2) 진공밀봉을 위한 quartz tube 실링, (3) 1차 합성 및 균질화를 위한 용해, (4) ingot 제조를 위한 crystal 성장(zone melting)까지의 공정을 포함한다. 소재 균질성(∼80%) 및 성능은 상대적으로 우수하나 꺾임 강도가 낮고(20 MPa 이하) ingot으로부터 열전소자(leg, thermoelectric pellet)를 제조하는 최대 수율이∼41%로 낮은 단점이 있다(Fig. 4, Ingot의 상하부 절단에 의한 손실 20%, slicing에 의한 손실 16%, dicing에 의한 손실 18% 및 선별 손실 25%).
상술한 4단계 세부공정은 각각 다음과 같은 과정으로 진행된다. (1) 조성비에 따른 원료금속의 준비: Ingot 제조 과정 중에 위 부분에 Te-rich phase가 형성되는 문제가 발생할 수 있어, 실제 칭량 시에 Te를 3 wt.% 정도 추가로 첨가한다. 제조업체에 따라 차이가 있으나 1 kg batch 이상 수준으로 제조한다. 원료금속의 순도는 모듈의 성능/가격에 따라 다르나, 고사양 모듈의 경우 5N(99.999%) 이상의 고순도 원료금속 사용이 요구된다. 열전소재는 기본적으로 반도체 소재이므로 극미량의 불순물에 의해서도 특성이 변화할 수 있어, 동일한 5N 순도의 원료금속을 사용하더라도 열전특성에 영향이 있을 수 있으므로 원료금속의 선택이 매우 중요한 요소가 된다. (2) 진공밀봉을 위한 초자 가공: 일반적인 quartz tube를 사용하며, 원료와 quartz tube와의 반응성이 거의 없어 carbon 보호층 코팅을 위한 acetone cracking 등의 작업은 필요 없다. 수소/산소 torch를 이용한 밀봉을 사용하며 고진공을 위해 diffusion 펌프를 사용하는 것이 바람직하다. 일반적으로 수작업으로 진행하나, 2 ways 또는 3 ways torch 설치 및 회전모터를 이용하여 공정 일부를 자동화하는 것도 가능하다. (3) 1차 합성 및 균질화를 위한 용해: 금속원료 간 증기압에 큰 차이가 있어 ingot 제조 전에 1차 용해 및 균질화가 필요하다. p형 및 n형 소재 모두 융점이 600°C 이하로 통상적인 용해온도는∼800°C이며(고융점 첨가제를 포함하는 경우∼1,100°C 이상에서 진행[7]), 균질화를 위해서는 rocking furnace의 사용이 필요하다. 조건에 따라 차이가 있을 수 있으나, 2–3 시간 용융으로 ingot 제조에 필요한 균질도를 얻을 수 있다. (4) Ingot 제조를 위한 crystal 성장: Zone melting 설비를 이용한다. Multi-channel의 설비를 사용하면 동시 제조가 가능하며, ingot의 중량, 크기 등에 따라 다를 수 있으나, 직경 약 25 mm 길이 약 300 mm 크기의 ingot 기준으로 약 12 시간 동안 제조할 경우 균일도 75% 이상의 ingot 제조가 가능하다.
Zone melting 공정으로 제조한 상용 p형 Bi0.5 Sb1.5 Te3 ingot의 경우 상온에서 전기전도도∼1000 S/cm, 제벡계수∼215 μ V/K, 열전도도∼1.4 W/mK의 특성을 나타내며 zT는 약 1.0 수준이다.[8] 반면, n형 Bi2 Te2.7 Se0.3(전하밀도 증가를 위해 I 미량 첨가) ingot의 경우 상온에서 전기전도도∼1050 S/cm, 제벡계수∼-200 μ V/K, 열전도도∼1.5 W/mK의 특성을 나타내며 zT는 약 0.9 수준이다.[7] 경우에 따라 p형 소재에 Se을 첨가하거나 n형 소재에 Sb를 미량 첨가한 조성을 제조하기도 한다. 한편, zone melting 공정으로는 결정배향성이 큰 ingot 형태의 소재가 제조되기 때문에 기계적 신뢰성이 낮아(Bi-Te계 소재를 ingot 형태로 제조할 경우 약한 van der Waals 결합의 c축 배향 구조가 되어 파괴가 쉽게 발생하는 벽개면이 정렬되어 강도(꺾임 강도 및 압축 강도)가 낮음) 고 신뢰성 부품을 요구하는 응용을 위해서는 소재의 강도 증대가 요구된다. 이에 따라 열전성능과 강도 증대를 목적으로 다결정 벌크 소재를 제조하는 공정이 개발되고 있다.
2.2 다결정 벌크 소재 제조 공정
2.2.1 분말 제조 공정
다결정 벌크 소재 제조를 위해서는 우선 분말을 제조하는 것이 필요하다. 분말 제조 방법 중 ball milling 설비를 이용한 기계적합금화(mechanical alloying)는 원료금속으로부터 직접적으로 열전소재 조성의 화합물 분체를 제조할 수 있다.[9,10] 기계적합금화는 공정이 간단하고 양산성 및 성능 재현성이 우수하며, 상온에서 진행할 수 있는 등의 장점이 있으나 ball로부터의 불순물 유입, 공정 중 산화 등에 의한 특성 저하 문제를 근본적으로 해결하는 것이 어려운 단점이 있다. 따라서 원료금속의 고순도를 유지하고 산화를 최소화하기 위해서는 용융법 기반의 공정이 필요하다. p형 소재의 경우∼1000 S/cm 수준의 전기전도도 구현을 위해서는 Bi와 Sb의 원료금속 비율을 zone melting에 의한 ingot 제조 공정과는 다르게 칭량하는 것이 필요하며, 이 경우 Te의 추가 첨가는 일반적으로 1 wt.% 수준이다. n형 소재의 경우에 Te의 추가 첨가는 최종 소결체에서 Te-excess 조성을 형성할 수 있고, 이는 전하밀도의 급격한 감소 또는 증가를 유발하므로 화학양론에 정확히 맞추어 원료를 칭량하는 것이 중요하다. Quartz tube sealing은 ingot 제조 공정과 동일하게 진행하며, 용융은 rocking furnace로 진행하는 것이 바람직하나 box furnace에서 진행해도 최종 벌크 소재의 성능에는 크게 영향을 주지 않는다. 냉각 후 수득한 ingot 형태의 원료합금을 ball milling으로 분쇄하여 열전소재 분말을 제조한다. Fig. 5에 box furnace에서 제조한 샘플과 planetary ball mill로 제조한 분말의 사진을 나타내었다.
Milling energy가 상대적으로 큰 고에너지 설비를 이용할 경우 10분 내에 평균 5-10 마이크로미터 수준으로 분쇄가 가능하며, 산화 방지를 위해서는 glove box에서 용기를 sealing 하는 것이 바람직하다.
2.2.2 나노구조화 및 결함제어 분말 제조 공정
나노구조화 및 결함제어가 열전소재의 성능증대에 효과적임이 이론적-실험적으로 증명되면서[11-13], 수 – 수십 nm 크기의 분말을 제조하거나 nm 크기의 결함구조를 포함하는 분말을 제조하는 공정기술 개발이 진행되고 있다. 나노 및 결함 구조 분체 제조를 위한 bottom-up 공정으로는 용매열합성법(solvothermal method)과 습식 화학반응법(wet-chemical reaction) 등이 개발되었다. 용액 기반의 bottom-up 공정은 매우 균일하게 제어된 크기와 형상의 나노분말 제조가 가능하다는 장점이 있어 벌크 소결체에서 나노분말의 특성 크기를 유지할 경우 매우 낮은 격자열전도도가 구현되고 있으며, 나노입자의 혼합에 의한 복합구조 제조로 캐리어필터링(carrier filtering) 효과에 의한 제벡계수의 증대 또한 구현할 수 있다. 그러나 제조 공정 중에 발생하는 입자 표면의 산화, 잔류 유기물 등의 문제 및 소결체의 낮은 상대밀도로 전기전도특성이 저하되는 단점이 있기 때문에 활용이 제한되고 있다.[14-16] 한편, 나노 및 결함 구조 분체 제조를 위한 top-down 공정으로는 high energy ball milling[7], melt spinning[17] 및 spark erosion[18] 공정 등이 개발되었다. High energy ball milling 공정은 나노분말 및 복합분말을 제조할 수 있는 간단하고 효과적이며 양산성 확보가 용이한 장점이 있다.[7,19] Bi0.5 Sb1.5 Te3 분말과 Cu acetate 분말을 혼합하고 환원 분위기에서 열처리를 진행하면 Fig. 6.a 에 나타낸 바와 같이 50 nm 크기의 Cu 나노입자가 Bi0.5 Sb1.5 Te3 분말 표면에 decoration된 복합분말을 제조할 수 있다. 또한 high energy ball milling 및 환원열처리 조건을 제어하면 Cu 나노입자의 크기를 수 nm 수준까지 감소할 수 있다(Fig. 6.b).[19,20]
Melt spinning 공정은 급속응고에 의해 리본, 스트립 또는 플레이크 형태의 금속합금을 제조하는 공정기술로, Fig. 7에 나타낸 바와 같이 고속으로 회전하는 Cu 휠 표면에 용융상태의 원료를 분사하여 1초에 10,000–10,000,000도 수준의 매우 빠른 냉각속도를 구현함에 의해 비정질로부터 nm 수준의 특성 크기를 갖는 구조를 형성할 수 있다.[21,22]
Melt spinning은 융융된 원료가 Cu 휠에 분사될 때 Cu 휠 표면과 접촉하는 contact surface에서 가장 빠른 냉각이 발생하고 챔버 내 분위기에 노출되는 free surface에서는 상대적으로 느린 냉각이 발생한다. 따라서 contact surface로부터 고체상이 형성되어 free surface 방향으로 성장하는 메커니즘으로 응고가 진행되므로 Fig. 8의 주사전자현미경(SEM, scanning electron microscopy) 사진에 나타낸 것과 같이 다양한 결함구조 형성이 가능하다. Fig. 8.a 에 나타낸 바와 같이 melt spinning으로 제조한 Bi0.5 Sb1.5 Te3 리본의 contact surface에서는 수십 nm 크기의 결정상이 관찰되며, free surface(Fig. 8.b)에서는 1 μ m 수준의 특성크기를 갖는 플레이트 형상 구조와 기공이 관찰된다. Fig. 8.c 에 나타낸 바와 같이 Cu 휠의 회전속도를 증가하면 free surface에 나타나는 특성크기가 감소하는 것으로부터 melt spinning 공정 조건을 조절하여 소재에 형성되는 결함구조의 특성 제어가 가능함을 알 수 있다. 또한, Fig. 8.d에 나타낸 것과 같이 Te를 과량 첨가한 Bi0.5 Sb1.5 Te3를 원료로 사용할 경우 상분리에 의해 Bi0.5 Sb1.5 Te3과 Bi0.5 Sb1.5 Te3-Te 공융조성이 동시에 형성되는 복합구조체를 제조할 수 있다.[17,20]
Fig. 8.
SEM images for a. contact surface and b. free surface of Bi0.5 Sb1.5 Te3 ribbon prepared by melt spinning fabricated at the linear Cu wheel rotating speed of 30 m/s. c. Free surface SEM image of Bi0.5 Sb1.5 Te3 ribbon prepared by melt spinning at fabricated at the linear Cu wheel rotating speed of 45 m/s. d. Free surface SEM image of heterostructured ribbon prepared by melt spinning at fabricated at the linear Cu wheel rotating speed of 40 m/s showing the Bi0.5 Sb1.5 Te3 platelets surrounded by the eutectic phase of Bi0.5 Sb1.5 Te3-Te mixture[17,20]
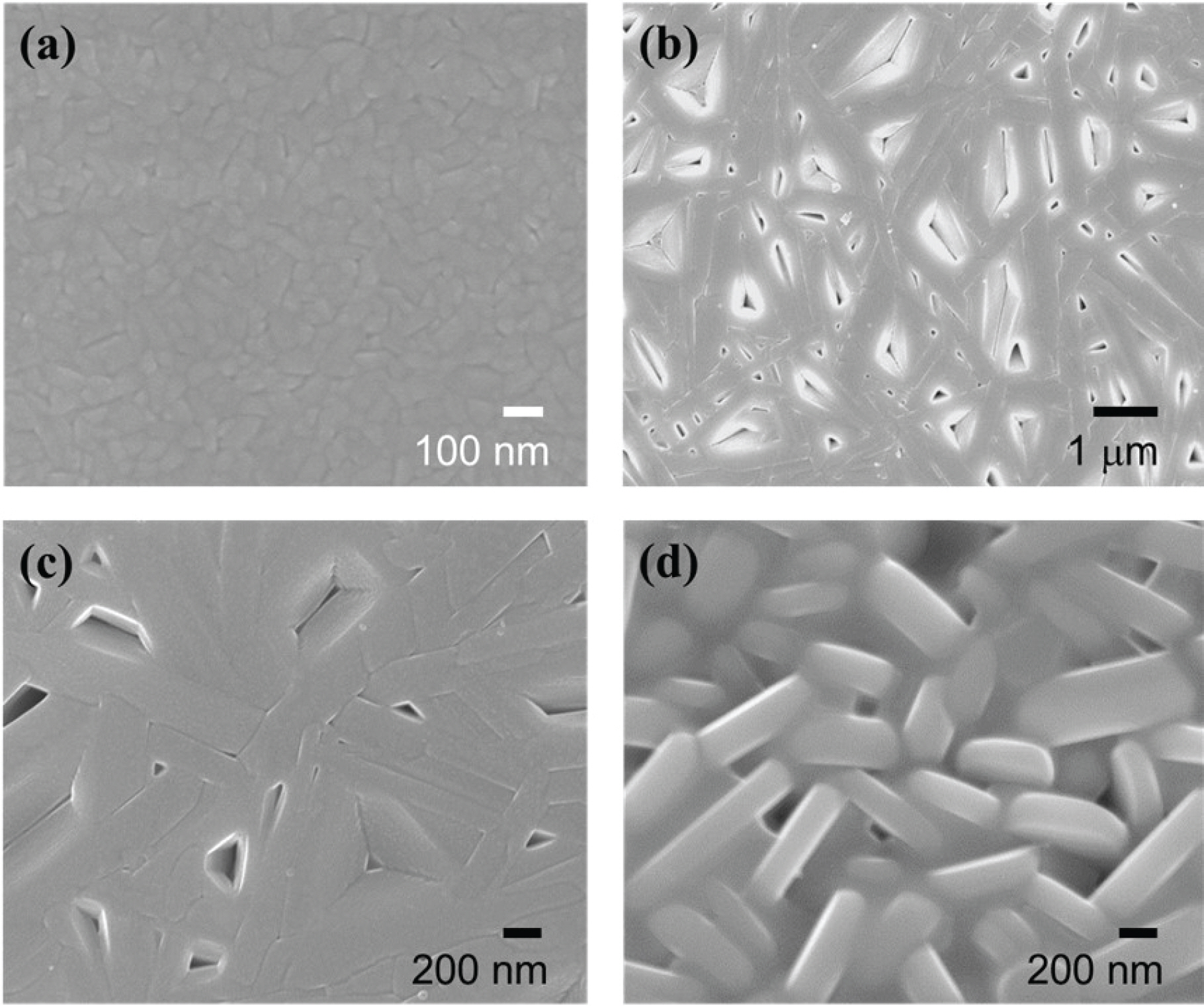
Melt spinning 공정 후 수득하는 소재는 일반적으로 리본으로, 분말 제조를 위해서는 추가적인 ball milling 공정이 필요하다. 급속 응고 공정의 한 종류인 spark erosion 공정도 나노 및 결함 구조 분말 합성에 효과적인 것으로 보고되었다.[18]
2.2.3 가압소결(pressure induced sintering) 공정
Bi-Te계 열전소재의 응용확대를 위해서는 zT 증대와 동시에 기계적 신뢰성 향상이 필요하여, 높은 강도가 보증되는 다결정 소결체 형태의 소재에서 높은 성능 구현이 필요함에 따라 관련 연구가 진행되고 있다. 다결정 소결체에서 높은 zT를 구현하기 위해서는 일반적으로 높은 상대밀도가(상대밀도가 낮으면 기공에 의한 열전도도 저감 효과가 있으나, 전기전도도 감소를 수반하여 zT 증대 효과가 없음) 필요하다. 따라서 소결 시 열에너지와 함께 압력을 인가하는 가압소결 공정인 hot pressing(HP) 및 spark plasma sintering(SPS)을 주로 사용한다. 용융-응고 공정에 의한 분말 합성 및 가압소결 공정에 의한 소결체 제조는 (1) 조성비에 따른 원료금속의 준비, (2) 진공밀봉을 위한 quartz tube 실링, (3) 1차 합성 및 균질화를 위한 용해, (4) ingot 기계적 분쇄 및 분급에 의한 분말 제조, (5) HP 또는 SPS를 이용한 가압소결체 제조까지의 공정을 포함한다. 열전소자 제조 시 상하부 절단이 필요 없어 zone melting 공정으로 제조한 inogt과 비교하여 높은 수율(∼50%)을 얻을 수 있다. 상술한 5단계 세부 공정 중 (1) – (3)은 zone melting 공정과 거의 유사하다. (4)의 공정을 위해 planetary ball mill 또는 vibration ball mill과 같은 고에너지 mill을 사용할 수 있다. Vial과 ball의 재질은 일반적으로 SUS를 사용하며, ball의 크기는 직경 약 5 mm이고 ingot의 중량 대비 10배 정도를 사용한다. Planetary ball mill의 경우 회전속도를 200 rpm 이상으로 설정하고 1시간 동안 분쇄를 진행하며, vibration ball mill의 경우 상대적으로 에너지가 높아 5분간 분쇄를 진행하면 50 μ m 크기 이하의 분말을 제조할 수 있다. Vial 내에 ingot을 장입하기 전에 유발을 이용하여 작은 알갱이 형태로 1차 분쇄하면 효과적이며, ball milling 공정 시 온도 증가에 의한 산화 발생을 방지하기 위해 vial에 ingot 장입을 glove box 내에서 진행하는 것이 바람직하다. 분쇄 후 수득한 분말을 sieve로 분급하여 소결체 제조를 위한 분말을 제조한다. (5)의 공정을 위해 graphite mold를 이용한다. 샘플 수득의 편의성 및 몰드와의 반응 방지를 위해 몰드의 안쪽 전면에 0.2 mm 수준 두께의 carbon sheet를 부착하고, 샘플과 닿는 하부펀치의 상단면과 상부펀치의 하단면은 소결 후 샘플의 분리를 위해 BN 이형제를 스프레이를 이용하여 코팅하는 것이 좋다. 하부펀치를 몰드에 끼우고 분말을 장입한 후 상부펀치를 끼운 후 진공 또는 아르곤 분위기에서 HP 또는 SPS를 진행하며, 분말의 조성과 미세구조(분말에서의 나노 및 결함 구조를 소결 후 유지하기 위한 공정 제어가 필요함)에 따라 300-500°C 온도와 30-70 MPa의 압력 범위에서 1–5 분간 소결을 진행하는 것이 일반적이다. p형 Bi-Te계 소재의 경우, 상용 ingot을 분쇄하여 powder를 제조하고 HP 또는 SPS으로 소결체를 제조하는 것만으로도∼1.10 수준의 zT를 구현할 수 있다.[23] 그러나 이러한 소재 중 ingot과 비교하여 전기전도도가 낮은 경우(기본적으로 조성이 동일하므로 ingot과 소결체의 전하밀도는 동일하나, 소결체의 경우 c축 방향
으로의 결정 배향성 저하로 이동도가 낮음)에는 냉각모듈에 적용 시 높은 효율을 구현하기 어렵다. 이는 냉각모듈 구동 시 Peltier 효과에 의한 열 이동 이외에 방열부로 부터의 열 back diffusion과 열전소재 자체 발열에 의한 Joule heating이 복합적으로 고려되어야 하는데, Joule heating에 의한 열손실을 최소화하기 위해서는 소재의 전기전도도가 상온 기준 950 S/cm 이상이 요구되기 때문이다.(Equation 1로부터 전기전도도를 임의로 감소하면 열전도도의 전자/홀 기여분의 감소하여 zT가 증대될 수 있으나, 이는 실제 모듈에서 구현이 되지 않는 착시효과를 포함한 결과이므로 전기전도도 1000 S/cm를 기준으로 zT를 환산하여 평가하는 것이 필요) p형 소재의 경우 높은 강도를 목적으로 전기전도도를 ingot과 유사한 수준으로 제조 가능한 조성(Bi자리에 Sb의 비율을 증가하면 전하밀도 증가로 전기전도도 증대 가능)으로 HP에 의한 상용소재가 일부 생산되고 있다. n형 소재의 경우 다결정 소결체는 결정 및 열전특성의 이방성이 매우 크며, 소결체 제조 시 Te/Se 휘발에 따른 전하밀도의 불안정으로 ingot을 분쇄하여 소결하는 단순한 공정으로는 zT∼0.6의 매우 낮은 열전성능을 나타내어 새로운 소재개발 전략이 요구된다. 최근 Cu-intercalation(Fig. 3에 나타낸 van der Waals gap에 Cu가 intercalation된 구조를 형성하고 있음)에 의해 n형 Bi-Te계 다결정 소결체의 전하밀도 불안정 문제를 개선하였으며 impact deformation에 의한 나노그레인 구조 형성으로 zT∼1.1의 높은 열전성능을 구현하였다.[24]
2.2.4 열간압출(hot extrusion) 공정
Bi-Te계 열전소자 제조에는 Fig. 9에 나타낸 3가지 공정이 주로 활용되고 있다. 2.2.2에 기술한 바와 같이 zone melting으로 제조한 열전소자의 경우 기계적으로 매우 약한 벽개면이 정렬된 구조를 형성하여 꺾임 강도가 20 MPa 수준으로 매우 낮은 문제가 있다. 가압소결의 경우 꺾임 강도는 80 MPa 수준으로 높으나, n형 소재의 성능이 상대적으로 낮고 공정 비용이 높은 단점이 있다. 열간압출은 온도와 압력에 의해 입자의 유동성을 유발할 수 있으며, 봉상의 벌크 소재를 제조할 수 있다. 따라서 zone melting 공정과 가압소결 공정의 단점을 어느 정도 보완할 수 있는 공정으로 50 MPa 수준의 높은 강도를 구현할 수 있고 zone melting으로 제조한 소재와 비교하여 동등 수준의 성능을 구현하는 것이 가능하다. (1) – (4) 공정은 가압소결과 유사하며 열간압출을 위해 분말을 disc형태로 일축가압하여 성형체를 제조한다. 이후 성형체를 몰드(일반적으로 초경재질 사용) 상부에 위치하고 열간압출기를 이용하여 분말의 조성과 미세구조에 따라 300-500°C 온도와 1-10 MPa의 압력 범위에서 1분 이내에 열간압출을 진행한다.
2.2.5. 유사정형(near net shape) 열간압출 공정
열전소재 성능 증대를 위한 나노 및 결함 구조 분말 개발 동향과 zone melting, 가압소결 및 열간압출 공정의 특성을 고려하면 (1) 열전성능 증대를 위한 벌크 소재에서 분말의 나노/결함 특성 유지가 가능한 초고속 벌크 제조 공정, (2) 기계적 신뢰성 확보를 위한 다결정 벌크 제조 공정 및 (3) 열전소자 제조 수율 향상을 위한 유사정형 공정이 요구된다. 봉상의 열간압출체(hot extrudate)의 단면적을 현재 열전모듈에 사용되는 직육면체 형태의 열전소자 단면적과 동일하게 제조하면, Fig. 10에 나타내 바와 같이 slicing 공정만으로 열전소자 제조가 가능하기 때문에 수율을 80% 이상으로 향상할 수 있다.
Fig. 10.
Schematic illustration showing the fabrication process of thermoelectric pellets from near net shape hot extrudate
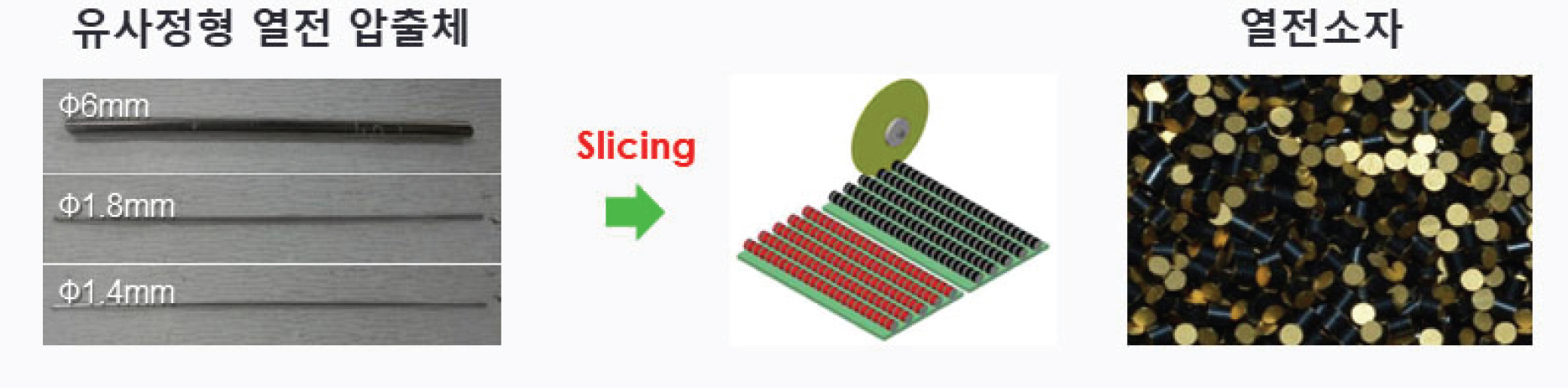
유사정형 열간압출을 위해서는 압출 설비와 몰드 개발이 요구된다. 공정 시 열에 의한 변형 및 표면 손상이 발생하지 않는 재질이 필요하며, 10초 이내(분말에서의 나노 및 결함 구조 유지를 위해 공정 시간 최소화가 필요함)에 높은 열전성능의 압출체 제조가 가능해야 한다. Fig. 11에 일반적으로 사용할 수 있는 압출설비와 몰드의 구조를 나타내었다.
유사정형 열간압출을 위한 분말은 2.2.1 및 2.2.2에 기술한 방법을 포함하여 다양한 기술로 제조할 수 있으며, Fig. 11의 설비와 몰드를 이용한 Bi-Te계 유사정형 열간압출체 제조 예는 다음과 같다. (1) 제조한 분말을 일축가압 설비로 disc 형태로 성형한다. (2) 성형체를 Fig. 11에 나타낸 sample 위치에 거치하고 heater를 이용하여 가열한다. (3) 상부 펀치를 이용하여 sample 에 압력을 인가한다. 이상과 같은 간단한 공정으로 Fig. 10에 나타낸 바와 같이 다양한 직경의 압출체를 제조할 수 있다. 압출체 제조 시 온도, 압력 이외에 몰드의 재질과 노즐의 형상이 중요한 요소가 된다. Fig. 12에 압출방향의 수직방향(perpendicular) 및 수평방향(parallel)에 대한 n형 Cu0.03 Bi2 Te2.7 Se0.3 압출체의 파단면 미세구조를 나타내었다.[25] 이를 통해 기공이 거의 없는 높은 상대밀도 구현 및 수평방향에서 zone melting으로 제조한 inogt에서 관찰되는 입자정렬 구조(높은 파워팩터를 구현하기 위한 미세구조 인자) 형성을 확인하여 공정을 최적화하는 것이 중요하다.
Fig. 12.
SEM images for the fractured surfaces of Cu0.03 Bi2 Te2.7 Se0.3 extrudate; a. perpendicular to the extrusion direction and b. parallel to the extrusion direction[25]
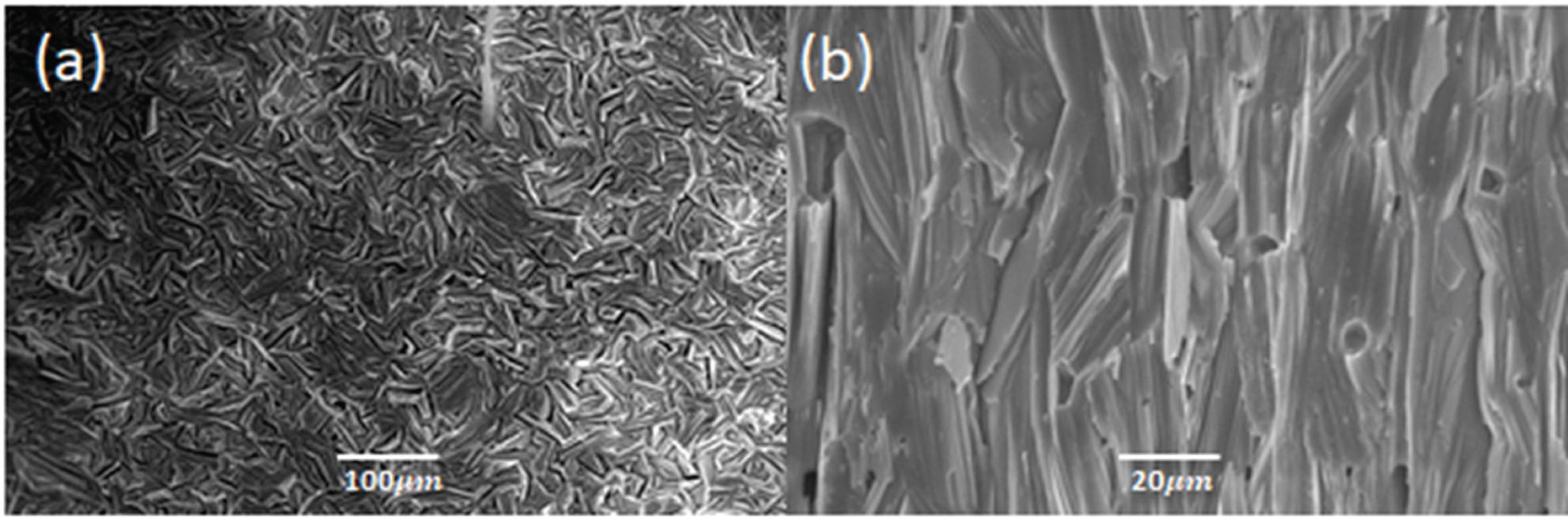
유사정형 열간압출체의 꺾임 강도는 50 MPa 이상으로 HP 또는 SPS로 제조한 소결체의∼80 MPa 보다는 낮으나 zone melting으로 제조한 ingot의∼20 MPa과 비교하여 매우 높은 신뢰성을 구현할 수 있다. Fig. 13에는 유사정형 열간압출 공정으로 제조한 p형 Bi0.44 Sb1.56 Te3 압출체 및 SPS로 제조한 Bi0.42 Sb1.5585 Ag0.0015 Te3 소결체의 파워팩터 온도의존성을 나타내었다. Bi0.44 Sb1.56 Te3 압출체는 300 K에서 최대 4.8 × 10-3 W/m-K2의 파워 팩터 값을 나타내었고, 이는 zone melting 공정으로 제조한 상용 ingot의 파워팩터(∼5.0 × 10-3 W/m-K2) 대비 96% 수준의 높은 성능이다(SPS 소결체 중 가장 높은 수준의 파워팩터를 나타낸 Bi0.42 Sb1.5585 Ag0.0015 Te3과 비교해도 7% 이상 향상된 값을 나타냄). 압출체의 경우 Fig. 12.b 에 나타낸 바와 같이 그레인이∼100 μ m 길이,∼10 μ m 두께의 다결정 구조를 형성하여 상용 ingot 대비 낮은 열전도도를 나타낼 것으로 예상된다(유사정형 열간압출체의 직경이 작은 이유로 레이저플레시법을 이용한 열전도도 측정이 어려움. 그레인 크기와 열전도도와의 상관관계를 고려하면∼1.3 W/m-K 수준의 열전도도가 예상됨. 상용 ingot의 경우 수 mm 수준의 그레인 구조를 형성하여 입계밀도가 낮은 이유로 포논산란이 제한되어 열전도도가 1.5 W/m-K로 높음).
Fig. 13.
Temperature dependent power factor of a. Bi0.44 Sb1.56 Te3 hot extrudate and b. Bi0.42 Sb1.5585 Ag0.0015 Te3 SPSed bulk
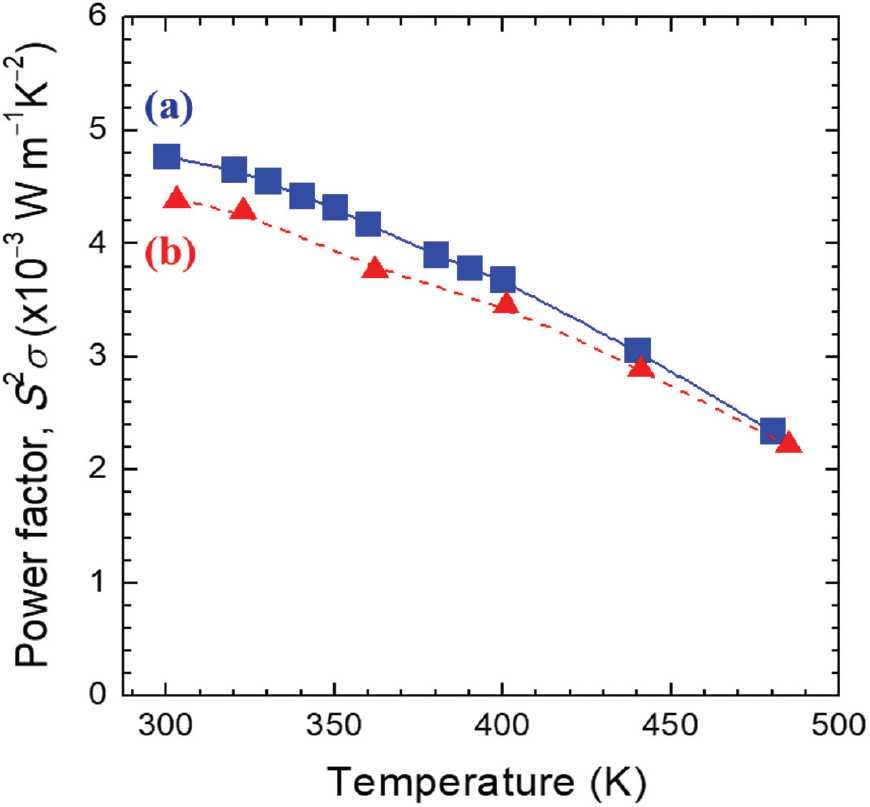
이상과 같이 제조한 유사정형 압출체는 열전소자에 요구되는 단면적을 갖으며 봉상으로 제조되기 때문에 높은 성능, 높은 기계적 신뢰성, 높은 소자 제조 수율을 동시에 만족하는 열전소재를 제조할 수 있는 공정기술을 제공한다. 최근 개발되고 있는 다양한 나노 및 결함 구조 분말에 유사정형 열간압출 공정을 적용하여 Bi-Te계 소재 기반 열전기술의 응용확대가 기대된다.
결론
무냉매-무압축기, 저진동-저소음, 고밀도 냉각 및 정밀온도 제어라는 냉각기술로의 장점 및 폐열활용 발전이라는 기술적 중요성에도 불구하고 열전기술은 소형냉각기, 온도제어, 특수발전 등에 국한되어 응용되고 있다. 이러한 한계를 극복하기 위해서는 무엇보다 열전소재의 성능 및 신뢰성 증대와 열전기술 적용에 대한 당위성-경제성 확보가 필수적이다. 최근 상용소재인 Bi-Te계 열전소재를 중심으로 성능 증대를 위한 연구-개발이 활발하게 진행되고 있으며, 조성제어, 나노구조화, 결함제어 등에 의해 성능 증대가 구현되고 있다. 또한 기존 zone melting 공정으로 제조한 소재의 성능-신뢰성 한계 극복을 위해 급속응고 기반의 분말 합성 공정과 가압소결 기반의 벌크 제조 공정 개발도 진행되고 있으나, 양산 시 성능 제한, 높은 공정 비용, 낮은 수율 등 실제 소재 생산 적용에는 많은 문제점을 나타내고 있다. 본 논문에서는 이러한 문제를 해결하기 위한 실효적인 전략으로 zone melting 공정의 장점을 발현함과 동시에 분말에서의 나노 및 결함 구조를 벌크 소재에서 유지할 수 있으며 열전소자 수득 효율을 80% 이상으로 향상할 수 있는 신공정 기술로 유사정형 열간압출에 대한 기술 정보를 제공하였다. 최근 소형 냉장고를 중심으로 생활가전에 대한 열전기술 적용이 확대되는 상황에서 유사정형 열간압출 기술은 상용 열전소자 제조에 적용되어 성능, 신뢰성, 경제성 측면에서 경쟁력을 제고할 수 있을 것으로 기대된다.