서론
Fig. 1.

Table 1.
범주 | 리튬 (Li) | 소듐 (Na) |
---|---|---|
원자량 (g mol-1) | 6.94 | 22.99 |
1가 양이온 반경 (Å) | 0.76 | 1.02 |
표준 환원 전위 (V vs. SHE) | -3.04 | -2.71 |
융점 (° C) | 180.5 | 97.7 |
이온화 에너지 (kJ mol-1) | 520.2 | 495.8 |
지각 내 매장량 (mg kg-1) | 20 | 23.6×103 |
주요 분포 | 남미, 중국, 호주 | 광범위 |
탄산염 가격 ($ ton-1)[3] | 37,000 | 140 |
무게당 이론 용량 (mAh g-1) | 3861 | 1161 |
체적당 이론 용량 (mAh cm-3) | 2062 | 1131 |
본론
2.1 흑연 기반 음극 소재 연구
Fig. 2.

2.2 실리콘 기반 음극 소재 연구
2.3 하드 카본 기반 음극 소재 연구
Fig. 3.

2.4 금속 산화물 기반 음극 소재 연구
2.4.1 타이타늄 산화물계 음극 소재
Fig. 4.
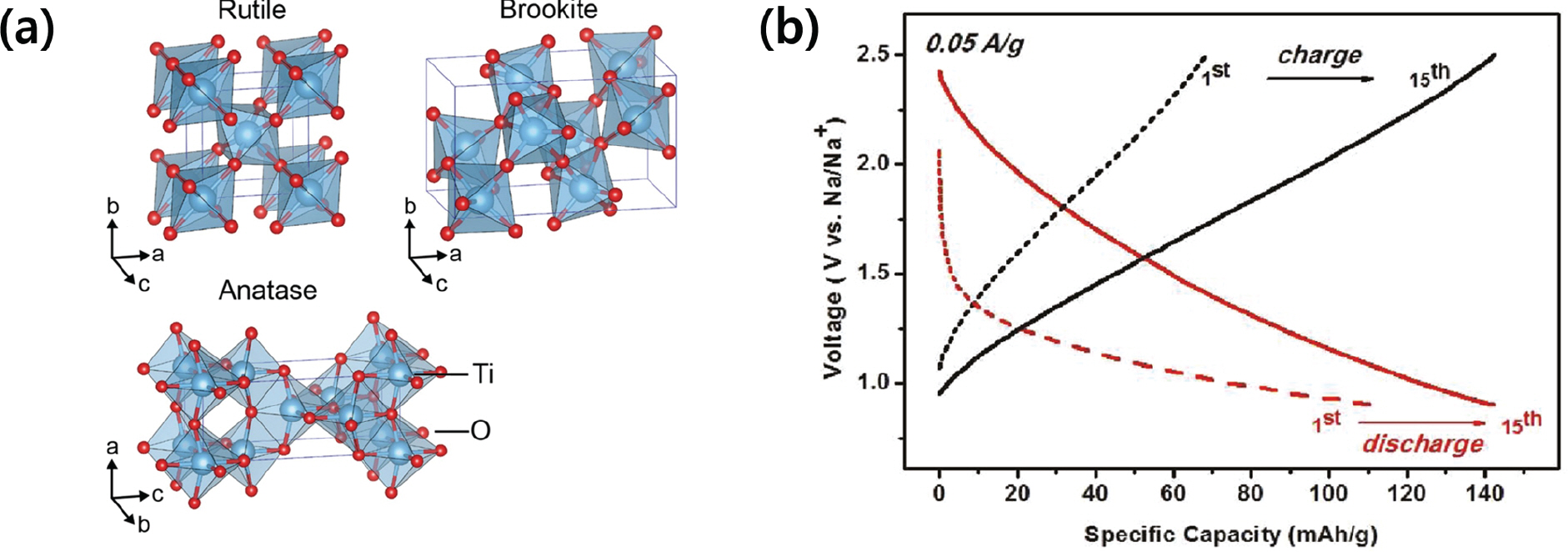
2.4.2 바나듐 산화물계 음극 소재
2.5 인 기반 음극 소재 연구
Fig. 5.
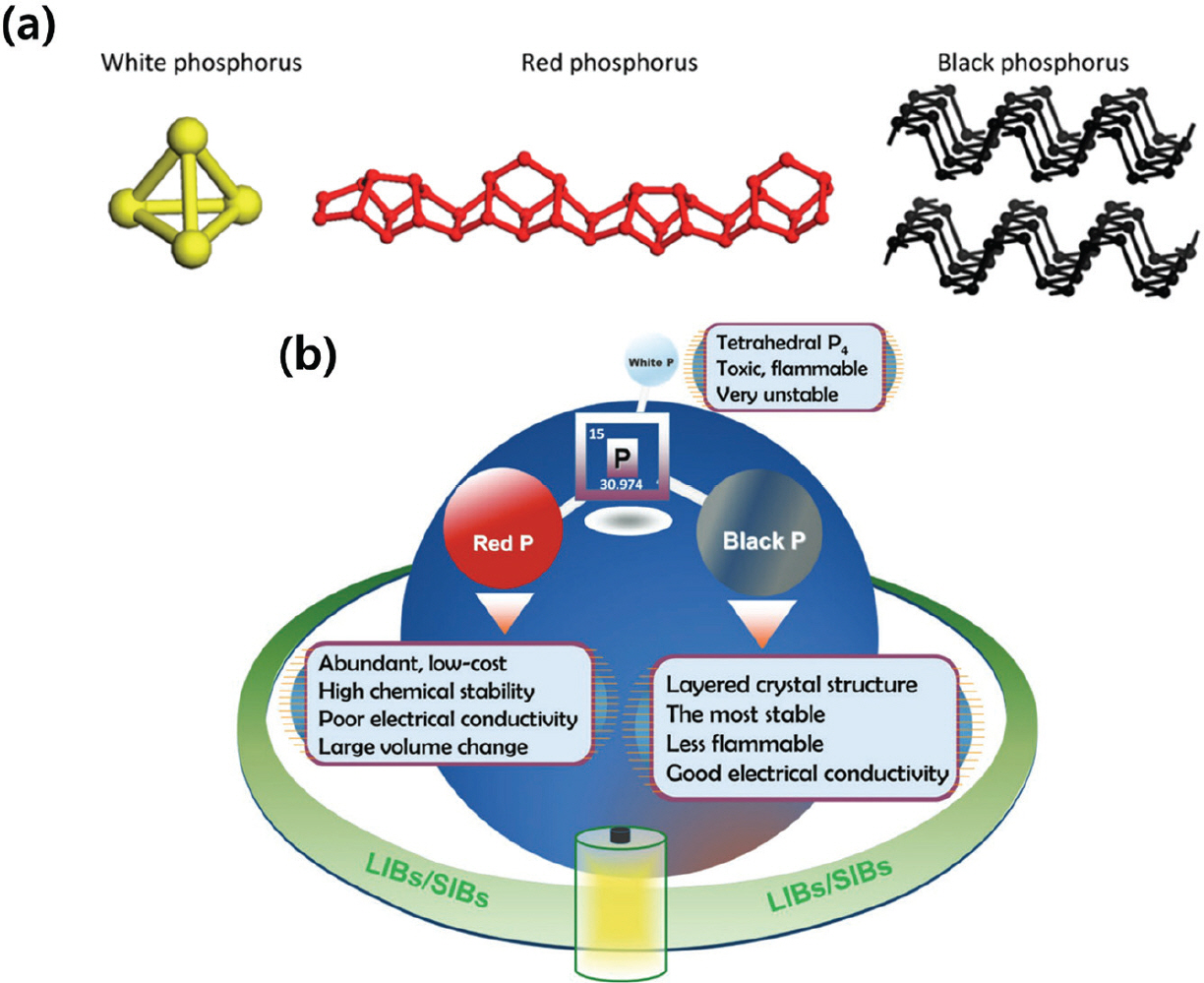
2.6 금속 인화물 기반 음극 소재 연구
2.6.1 초기 전이금속 인화물
Fig. 6.

2.6.2 후기 전이금속 인화물
Fig. 7.

2.7 금속 황화물 기반 음극 소재 연구
Fig. 8.
