금속 질화물 박막의 원자층 증착 및 반도체 분야 응용 연구 동향
Research Trends of Atomic Layer Deposition of Metal Nitrides and Their Applications in Semiconductor Industry
Article information
Trans Abstract
With the recent advances in nanotechnology and the semiconductor industry, the study of nitride thin films has become increasingly important in the fields of electronic devices, optical devices, and nanomaterials research. Various methods have been used to synthesize nitride thin films, among which ALD stands out as a deposition technique capable of yielding high-quality thin films at lower temperatures via sequential self-limiting surface treatments. As the need for high-quality thin film deposition at the nanoscale and highly conformal thin films has emerged, the deposition of metal nitride thin films by ALD has been actively researched, encompassing hafnium nitride, aluminum nitride, titanium nitride, zirconium nitride, and silicon nitride. In this review, we will discuss the current landscape of research pertaining to metal nitride thin films prepared by ALD.
1. 서론
최근 나노 기술 및 반도체 산업의 발전으로 인해, 질화물 박막에 대한 연구는 전자 소자, 광학 소자 및 나노 물질 연구 분야에서의 중요성이 더욱 부각되고 있다. 질화물은 전기 장치, 세라믹 등 광범위한 응용 분야에서 기존 제품을 대체할 수 있기 때문에 사용이 빠르게 증가하고 있는 추세이다. 금속 질화물은 높은 녹는점, 향상된 전자 특성 및 전기 촉매 특성과 같은 우수한 특성을 지니고 또한 우수한 기계적 강도, 열 전도율, 고온에서의 안정성, 내화학성 및 내마모성을 가진다. 이러한 특성으로 인해 슈퍼 커패시터와 같은 전기적 디바이스의 전극 재료[1-3]로 사용되거나 코팅 막[4,5], 게이트 유전체[6], 확산 배리어 층[1,7-9], 태양 전지[10-12], 수소 저장[13], 자성 물질[14] 등의 분야에 응용될 수 있다. 이러한 질화물 박막은 새로운 기술 발전을 주도하며, 다양한 연구 분야에서 높은 성능을 발휘할 것으로 기대된다. 따라서 본 논문에서는 이러한 금속 질화물의 중요성에 집중하였다. 과거에는 sputtering[4,15], activated reactive evaporation (ARE)[16], chemical vapor deposition (CVD)[17,18], metal-organic CVD (MOCVD)[19,20], low pressure CVD (LPCVD)[21,22], plasma-nhanced CVD (PECVD)[23], molecular beam epitaxy (MBE)[24], pulsed laser deposition (PLD)[25], 원자층 증착법(atomic layer deposition ALD)[3,26]와 같은 다양한 증착 기술이 질화물 박막의 합성에 활용되었다.
본 논문에서는 이러한 다양한 증착 방법 중에서도 특히 ALD에 주목하여, 질화물 분야에서의 연구 동향과 적용 가능성에 대해 탐구하고자 한다. ALD는 전구체 및 공반응물의 순차적 공급을 통해 한 사이클 당 한 개의 원자층이 적층되도록 하는 자기 제한적 표면처리 방법이다. 이를 통해 박막의 두께를 옹스트롬 수준에서 정밀하게 제어할 수 있으며 높은 품질의 박막을 얻을 수 있다. 특히, 기존 CVD나 physical vapor deposition (PVD) 공정에 비해 상대적으로 낮은 온도에서 공정이 가능하며, 자기 제한적 원리에 기반하여 우수한 단차 피복성을 제공한다. 뒤이어 기존의 thermal ALD보다 더 낮은 온도에서 박막을 증착하기 위해 플라즈마를 도입한 plasma-enhanced ALD (PEALD) 기술이 등장하였다.[27] PEALD는 플라즈마의 라디칼 또는 에너지 종을 통해 추가적인 에너지를 공급하여 반응성을 향상시키고, 낮은 온도에서도 높은 성장속도 (growth per cycle, GPC)를 유지할 수 있는 장점이 있다. 통상적으로 ALD 공정은 350° C 이하의 낮은 온도에서 수행된다. 성장이 포화되는 온도 범위인 ‘ ALD 온도 창’이 각 ALD 공정마다 존재하며, ALD 온도 창 외부의 온도에서 공정을 수행할 경우 전구체 응축 및 열분해 또는 급격한 탈착으로 인해 낮은 성장 속도 또는 원하지 않은 공정 결과를 초래할 수 있기 때문에 ALD 온도 창 범위 내에서 증착 공정을 수행하는 것이 중요하다.[27-29]
ALD는 오랜 시간 동안 연구되며 다양한 응용 분야에서 박막을 증착하기 위한 중요 기술로 자리잡았다. 특히, 반도체 산업의 소형화로 인해 원자 수준의 제어가 가능한 고품질 박막 증착 공정과 나노 스케일에서의 고도로 등각성이 우수한 박막의 필요성이 부각되면서, ALD를 통한 질화물 박막 증착에 대한 관심이 증가하고 있다. 본 논문은 질화물 ALD 증착 공정에 대한 깊은 이해를 위해, 주요 질화물 박막 소재인 하프늄 질화물, 알루미늄 질화물, 타이타늄 질화물, 지르코늄 질화물, 실리콘 질화물에 대한 ALD 연구 동향을 종합적으로 분석하고자 한다. 그리고 다양한 응용 분야에서의 연구 동향을 탐색하여, 현재 질화물 박막 연구의 상태를 파악하고 향후 발전 방향을 제시하고자 한다.
2. 금속 질화물 박막의 원자층 증착 및 연구동향
2.1 HfNx ALD
HfNx는 x값에 따라 결정 구조가 변화하는데, x가 이상적인 화학양론비인 1에 가까우면 rock-salt 구조의 HfNx (δ-HfN)가 되고 x가 증가할수록 cubic Th3 P4 구조의 HfNx (c-Hf3 N4)으로 점차 전환된다.[30] δ-HfN 는 낮은 비저항을 갖고 불투명하며, c-Hf3N4는 비저항이 높기 때문에 절연성을 가지며 투명하다. 또한, HfNx은 녹는점이 3305° C 로 높고, 0.82 eV의 좁은 전기적 밴드 갭[31]과 34.9 meV의 넓은 포노닉 밴드 갭[10,32]을 갖는다고 알려져 있다. 이러한 특성들로 인해 HfNx은 주로 metal-oxide-semiconductor (MOS) 디바이스[19,33-36], 슈퍼 커패시터[2]와 같은 전기적 디바이스에서 금속 전극으로 사용되거나 코팅 막[4,5,37], 핫 캐리어 태양전지[10-12,38] 분야에 응용되어왔다. HfNx는 현재까지 sputtering[4,37,39-41], ARE[16], CVD[42,43], MOCVD, ARE[16], CVD[42,43], MOCVD[19,44,45]와 같은 다양한 증착법을 통해 연구되어왔다.
HfNx을 ALD로 증착하기 위한 Hf 전구체로는 주로 metal alkylamides 계열의 Tetrakis(dimethylamido) hafnium(IV) (TDMAHf), Tetrakis(ethylmethylamido) hafnium(IV) (TEMAHf), Tetrakis(diethylamido) hafnium(IV) (TDEAHf)가 사용된다. 2004년 Becker et al.은 앞서 언급한 세 가지 Hf 전구체와 공반응물을 NH3로 사용하여 Si 기판 위에 150-250° C의 증착 온도에서 각각 Hf3N4를 성장시켰다.[46] 이때 TDMAHf으로 증착한 Hf3N4에서 가장 산소 오염이 적었기 때문에 NH3에 대해 TDMAHf의 반응성이 가장 크다고 보고하였다.[46] 다음 해인 2005년에 Xu et al.은 동일하게 전구체로 TDMAHf를 사용하고 공반응물로 NH3와 H2O을 사용할 때의 Density functional theory를 각각 계산하였고, NH3가 H2 O보다 전구체와의 리간드 교환을 위한 에너지 장벽이 더 높기 때문에 소량의 H2 O라도 시스템 내에 존재한다면 HfNx 박막에 상당한 양의 산소를 발생시킬 것이라고 보고하였다.[47] 또한, Ryoo et al.은 최근에 Si 기판 위에 전구체와 공반응물로 TEMAHf와 NH3를 사용하여 HfNx ALD를 진행하기 전, 전세척 공정으로 기판과 챔버 내 산소를 제거하면 HfNx 막 내에 산소 함량이 40-50%에서∼20%까지 감소되는 것을 확인하였다.[48] 추가로, 증착 온도가 200° C일 때 TEMAHf과 NH3 펄스 시간에 따른 박막의 성장 속도가 0.13 nm/cycle로 포화되는 것을 통해 해당 ALD 공정이 자기제한적 성장인 것을 보여 주었다.[48] 이러한 문헌에서의 결과들은 Alkylamides 계열 Hf 전구체와 NH3와 같은 N2 소스를 공반응물로 이용하여 ALD를 통해 HfNx 증착 시에 HfONx가 되지 않기 위해서는 챔버, 기판, 캐리어 가스 내에 잔여 산소나 H2 O의 제거가 매우 중요함을 보여준다.
NH3를 공반응물로 이용하여 증착한 HfNx 막은∼106 µΩ cm의 높은 비저항을 가지게 된다.[48] 하지만, 금속 게이트 전극으로 사용하기 위해서는 비저항이 낮은 HfNx를 증착해야 하기 때문에 반응성이 높은 플라즈마를 사용한 연구들이 진행되었다. 2006년 Kim et al.은 SiO2(300 nm)/Si 기판 위에 증착 온도 175° C에서 TDMAHf 전구체에 H2 플라즈마를 공반응물로 사용해 150 W의 플라즈마 파워로 PEALD를 통해 HfNx를 증착하였다.[49] 증착된 HfNx 박막의 성장 속도는 0.09 nm/cycle로 포화되어 ALD의 자기제한적 반응을 확인하였고, 비저항 값이 6700 μΩ cm인 저저항 HfNx를 얻었다.[49] 그 뒤에 Consiglio et al.은 SiO2/Si(100) 기판 위에 TEMAHf 전구체에 공반응물로 H2 플라즈마를 사용하여 250° C로 증착한 HfNx에서 플라즈마 파워가 600 W일 때 플라즈마 펄스 시간에 따른 성장 속도가 0.14 nm/cycle로 포화되고, 플라즈마 파워가 200 W에서 600 W로 증가하면서 N:Hf 비율이 감소함에 따라 비저항 값이 2327 μΩ cm까지 낮아짐을 보여 주었다.[33] 이러한 저저항 HfNx을 금속 게이트 전극으로 사용하여 4.63 eV의 중간 갭 일함수 값을 얻었다.[33] 앞서 반응성이 높은 플라즈마를 이용하여 전도성이 있는 HfNx를 증착한 결과를 봤지만, NH3 플라즈마와 H2 플라즈마로 증착한 HfNx의 비저항 값을 비교하였을 때 각각∼1.5 Ω cm,∼770 μΩ cm으로 NH3 플라즈마는 여전히 높은 비저항 값을 가진다.[50] 이러한 이유는 H2 플라즈마로 성장한 HfNx 막에서는 질소 함량에 대부분 전구체 리간드의 질소 성분이 기여하고 있지만, NH3 플라즈마는 전구체 리간드 뿐만 아니라 NH3 플라즈마 자체가 질소 성분을 포함한 공반응물이기 때문에 HfNx 막에 더 많은 질소를 공급하여 Hf3 N4 상을 형성시키기 때문이다.[50] ALD를 통해 성장시킨 HfNx 막에서 전도성을 원한다면 H2 플라즈마를 하는 것이 유리하지만, 막의 퀄리티 측면에서는 NHx 라디칼이 막 내의 탄소 불순물을 제거해주기 때문에 NH3 플라즈마가 유리하므로 원하는 HfNx의 특성에 따라 다양한 플라즈마 가스를 사용할 수 있다.
강유전성을 갖는 HfNx 박막이 개발된다면, HfO2 강유전층이 metal-ferroelectric-semiconductor field-effect-transistor (MFSFET)에 응용된 것처럼 MFSFET에도 적용할 수 있을 것으로 기대된다. 하지만, 현재까지 강유전성 HfNx 박막을 보고한 논문은 Ohmi et al.의 논문이 유일하다.[34,51] Ohmi et al.은 p-Si 기판 위에 HfN1.5와 HfN0.5 박막을 sputter로 증착한 뒤 400° C에서 post-metallization annealing을 해 주어 rhombohedral 상의 HfNx을 얻었고, HfN0.5에 해당되는 게이트 전극의 strain 영향으로 HfN1.5 박막이 강유전성을 갖게 되면서 MFS 구조를 제작하였음을 보여 주었다. 이러한 결과는 준안정상인 rhombohedral 상의 HfO2에서 strain이 걸릴 때 강유전성을 가지는 이전 연구 결과[52,53]와 비슷하며, ALD를 통해 증착하는 HfNx 박막도 strain이 걸린 rhombohedral 상이 된다면 강유전성을 얻을 수 있다는 가능성을 열어 주었다.
2.2 AlNx ALD
AlNx는 넓은 직접 밴드 갭 구조 (6.2 eV)[54], 높은 열 전도율 (2.85 W/cm⋅ K)[55]을 특징으로 하며, 이는 자외선 발광 장치[56], 발광 다이오드[57] 등의 전자 및 밴드 광전자 장치에서 유망한 소재로 주목받고 있다. 압전 재료로서 압전 효과를 통해 기계적 압력을 받으면 전하를 생성하는 특성을 가진다. 이러한 큰 압전 계수 (5.1 pm⋅ V-1)[58]와 낮은 비저항으로 인해 micro-electron mechanical systems(MEMS)의 공진기[59] 및 나노 에너지 발전기[60]로 사용되어 왔다. 또한 높은 유전 상수 (9.2)[61]와 전기 비저항 (1011 Ω⋅ m)[62], 그리고 우수한 기계적 강도, 열적 및 화학적 안정성을 바탕으로 high-k 게이트 유전체[6], MEMS 액추에이터[63], 아이솔레이터[64], resistive random-access memory의 resistive switching layer[65]와 같은 다양한 응용 분야에서의 연구를 촉진하고 있다.
Al2 O3의 열탄소 환원법[66], Al의 직접 질화법[67], AlCl3 또는 기타 유기 금속 전구체와 NH3 반응에 의한 기체상 합성[68] 등 다양한 AlN 증착 방법이 보고되어 왔다. 특히 MBE[24], MOCVD[20]와 같은 epitaxial AlN 제조 공정은 일반적으로 900° C 이상의 고온을 필요로 하였다. 2004년 Liu et al.은 thermal ALD와 PEALD를 통한 결정질 AlN 박막의 증착에 대한 연구를 발표하였다.[69] Trimethyl aluminium (TMA)와 NH3를 전구체로 사용하였으며, Si(100) 기판에서 200-470° C의 증착 온도로 thermal ALD와 PEALD 공정을 진행하였다. 이때 플라즈마 파워는 50-300 W를 인가하였다. Thermal ALD와 PEALD 모두에서 증착 온도에 따라 증착 속도가 크게 증가하는 경향을 보였다. 420° C에서 thermal ALD와 PEALD로 증착한 AlN의 성장 속도는 각각 1 Å/cycle, 1.5 Å/cycle로, PEALD를 사용할 때 thermal ALD에 비해 훨씬 더 높은 증착 속도를 나타내며, 동시에 증착 온도를 효과적으로 낮출 수 있었다. 35:1의 높은 종횡비를 가진 트렌치 구조 웨이퍼에서 thermal ALD를 통해 100%의 단차 피복성을 달성하였으며, 양 증착 공정 모두 370° C에서 470° C 사이의 온도 범위에서 (100) 방향을 가진 결정질 AlN을 증착하였다. 특히 X선 회절을 통해 PEALD 샘플의 (100) 피크가 thermal ALD 샘플의 피크보다 선명하다는 결과를 확인하여 PEALD로 증착된 필름이 더 높은 수준의 결정화를 나타낸다는 것을 관찰하였다. 이 연구에서는 thermal ALD와 PEALD 공정 모두 좋은 자기 제한적 반응을 보이지 않았다. 이를 NH3의 강한 표면 흡착 반응에 의한 것으로 보고, 다양한 온도에서의 NH3 흡착/탈착 연구에 대한 필요성을 제시하였다.[69]
같은 해 Lee et al.은 Aluminium chloride (AlCl3) 및 NH3/H2 플라즈마를 사용한 PEALD를 통해 염소 및 수소 불순물의 농도가 각각 0.23 및 2.01 at.%인 AlN 박막을 증착하였다.[70] 해당 공정은 Si(100) 기판에서 증착 온도 350° C, 플라즈마 파워 150 W의 조건에서 진행되었다. 성장 속도는 0.042 nm/cycle로 포화되었으며, 박막의 두께는 반응 사이클 수에 비례하여 증가하는 것을 관찰하였다. NH3는 N– H 결합의 강도로 인해 성장 표면에서 해리 효율이 낮은 경향이 있다. 이 문제를 극복하기 위해 일반적으로 고온 및 높은 압력 조건에서 NH3를 사용해왔다. 해당 연구에서는 NH3/H2 플라즈마를 사용하여 증착 온도를 낮추면서도 우수한 증착 효율을 유지했다. 동시에 플라즈마는 AlCl3에서 Cl을 추출하는 환원제 역할을 수행했다. 이러한 과정을 통해 산화 방지 특성이 우수한 AlN 박막 증착이 가능함을 보고하였다.[70]
ALD는 본질적으로 저온 공정이기 때문에 highly-ordered 필름을 성장시키는 데에는 적합하지 않다. 그러나 ALD 성장 레시피를 일부 조정하거나 다른 기판을 사용함으로써 필름 결정성에 영향을 줄 수 있다. 따라서 Banerjee et al.은 원격 플라즈마 반응기를 이용하여 다양한 공정 및 기판 조건에서 AlN의 결정성 변화를 분석하였다.[71] 동시에 원격 플라즈마 반응기를 사용하여 플라즈마로 인한 Si(111) 기판 또는 성장 중인 AlN 막의 영향을 최소화하여 PEALD 공정을 효과적으로 유지하였다. 이때 전구체로 TMA와 NH3 플라즈마를 사용하였으며, 2000 W의 플라즈마 파워를 사용하였다. 350° C의 증착 온도에서 0.1 nm/cycle의 성장 속도를 기록하였으며, 300-350° C 범위가 ALD 온도 창임을 확인하였다. 성장된 AlN 필름의 조성을 측정한 결과, 약 46%와 53%의 Al/N 조성을 보였으며 산소 및 탄소 불순물 농도 또한 2% 미만의 낮은 수준을 기록했다. Grazing incidence x-ray diffraction 스캔 결과로는 Si(111) 기판에서의 성장층이 다결정이며, hexagonal (wurtzitic) 결정면을 나타내는 것을 관찰하였다. 또한 더 높은 플라즈마 파워나 온도에서 증착하면 (0002) 면의 형성이 약간 증가하였으며, 경사각이 높아질수록 (0002) 면의 형성이 두드러짐을 확인하였다. Si(100) 및 SiO2 기판 위에 증착하면 (0002) 면의 수직 성장이 감소하여 Si(111)이 columnar hexagonal AlN 성장에 더 나은 기판임을 시사하였다.[71]
이전 연구에 따르면 NH3와 TMA를 사용하는 AlN ALD는 300° C 이하의 온도에서 불완전한 반응을 나타내고, 공정 과정에서 부산물을 완전히 제거하려면 450° C 이상의 고온 공정이 필요하다.[72] 이 문제를 해결하기 위해 2020년 Jung et al.은 질소 공급원 NH3의 대체제로서 반응성이 높은 hydrazine (N2 H4)를 제시하였고, 175-350° C의 저온에서 thermal ALD를 통한 AlN 박막 증착을 성공적으로 시연하였다.[72] 이때 Si(100) 기판을 사용하였고, Al 전구체로는 TMA를 사용하였다. 225° C에서 증착된 AlN 필름은 표면이 산화되는 것을 방지하기 위해 표면에 4 nm 두께의 실리콘 질화물 캡핑 층을 증착하였다. 해당 필름은 0.16 nm/cycle의 성장 속도를 나타내며 7.5%로 낮은 산소 함량을 가지면서 이상적인 조성비에 가까운 1:1.1의 Al 대 N 조성비를 나타냈다. 300° C의 증착 온도에서 성장 속도는 NH3보다 약 2.3배 높은 0.25 nm/cycle를 달성하였고, 탄소 및 산소 불순물 농도 또한 개선되었다. 350° C에서 증착한 AlN 필름의 refractive index는 1.98로 증착된 AlN이 고품질이라는 사실을 증명하였다. 따라서 N2 H4가 NH3를 대체할 수 있는 질소원이라는 가능성을 보여 주었다.[73]
ALD 공정은 표면 화학 반응에 의존하기 때문에 기판 의존성을 나타낸다. 필름의 균일성을 초기부터 효과적으로 제어하기 위해서는 다양한 기판에서의 핵 생성 및 성장 거동에 대한 이해가 필요하다. 특히 AlN/GaN 조합은 GaN 기반 전력 전자기기 응용에서 주목받고 있으며, 많은 논문에서 AlN/GaN 시스템에 대한 연구가 진행되어 왔다. 그러나 상이한 기판에 대한 AlN 박막의 핵 생성 및 성장 동역학은 여전히 잘 알려져 있지 않아 해당 연구에 대한 필요성이 제기되었다. Yun et al.은 Si 및 TiN 기판에서 AlN 막의 핵 생성 및 성장 거동을 조사하였다.[74] 전구체로 TMA와 NH3를 사용하였고, 295-342° C의 증착 온도에서 공정을 진행하였다. 322° C의 증착 온도에서 Si 기판은 기판 억제 성장으로 인한 핵 생성 지연으로 초기에는 0.28 Å/cycle로 낮은 성장 속도를 보였지만, 사이클 수가 증가함에 따라 1.52 Å/cycle로 성장 속도 또한 증가하였다. 대조적으로 TiN 기판에서는 1.62 Å/cycle로 핵 생성 지연 없이 일정한 성장 속도 선형 성장을 관찰하였다. 아레니우스 플롯의 기울기를 기반으로 ALD 반응에 대한 활성화 에너지를 계산했을 때 포화 Si (82.66 J/mol) 또는 TiN 기판 (68.02 J/mol)보다 초기 Si에서 111.91 J/mol로 더 높은 활성화 에너지가 나타났고, 이는 초기 Si 기판 상에서 AlN 필름의 ALD 반응을 위해 더 많은 양의 열 에너지가 필요하다는 것을 나타낸다. 추가로 Si 기판에서의 초기 성장 속도는 0.52 Å/cycle, TiN 기판에서의 초기 성장 속도는 2.09 Å/cycle로 NH3 전처리를 통한 NH3의 해리 흡착은 두 기판 모두에서 초기 핵 생성 단계에서의 성장 속도를 향상시킬 수 있음을 확인하였다. 따라서 기판에서의 NH3 해리가 AlN 필름의 후속 성장을 위해 균일한 핵을 만드는 데 매우 중요하다는 것을 시사하였다.[74]
장기간 동안 AlN은 분극 전환 능력이 부족한 비강유전성 물질로 인식되어왔다.[75] 최근 Lin et al.이 유일하게 AlN의 강유전성에 대한 연구 결과를 보고하였다.[75] 공정 조건으로는 TMA와 N2/H2 plasma를 사용하여 GaN/sapphire 기판에 증착을 진행하였다. 이 연구에서는 300° C의 저온에서 ALD를 사용하여 GaN 층에 증착된 AlN epitaxial 초박막의 강유전성 유도를 소개하였고, AlN/GaN 이종 접합의 분극-전압 (P-V) 및 전류-전압 (I-V) 특성을 조사하여 AlN epilayer의 강유전 스위칭을 확인하였다. 8 nm 및 10 nm AlN epilayer에서 각각 3.5 및 2.9 μ Ccm-2의 잔류 분극 (P r) 값을 얻었으며, 두 층 모두에서 안정적인 강유전성을 확인하였다. 그러나 동일한 방법으로 증착된 25 nm와 38 nm AlN epilayer는 상유전성을 가졌으며, 두꺼운 AlN epilayer 에서는 AlN/GaN 이종 접합에서의 격자 불일치에 기반한 강유전성 유도 메커니즘이 효과적이지 않음을 나타냈다. Reciprocal space mapping (RSM) 분석 결과, AlN 강유전성은 [0001]-oriented AlN epilayer의 out-of-plane 압축 변형과 in-plane 인장 변형에서 기인하는 것으로 밝혀졌고 AlN epilayer의 두께가 증가함에 따라 AlN 격자의 정렬 불량이 증가하여 AlN epilayer의 응력이 완화되었음을 알 수 있다. 이 연구는 complementary metal-oxide semiconductor (CMOS) 호환성을 가진 저온에서 제조된 AlN 초박막의 soft ferroelectric 특성을 발견하여, AlN/GaN 이종 접합에 기반한 저차원 강유전 시스템에 대한 새로운 기초 및 ALD 연구가 필요하다는 새로운 방향을 제시하였다.[75]
2.3 TiNx ALD
TiNx는 비저항이 낮고 열 안정성이 높기 때문에 주로 dynamic random-access memory (DRAM) 커패시터 구조에서 금속 전극[3,76]으로 쓰이거나 CMOS-compatible 물질[77-81], 확산 배리어 층[7-9]으로 사용되어왔다. TiNx을 증착하는데 주로 쓰이는 증착법은 sputtering [82-84], CVD[21,85,86], PLD[25,87,88]가 있다. Titanium tetrachloride (TiCl4)은 CVD를 통해 TiNx을 성장시키는데 많이 쓰이던 전구체이지만, 염소 불순물은 디바이스 성능을 저하시킨다고 익히 알려져 있다.[21,85] 따라서 염소 불순물이 없는 TiNx를 얻기 위해서는 다른 Ti 전구체의 사용이 필요하기 때문에 alkylamides 계열의 Ti 전구체들로 TiN CVD 연구가 진행되었다.[18,89,90]
ALD에서도 마찬가지로 TiNx 증착에 metal alkylamides 계열의 Ti 전구체가 주로 이용되어 왔다. Tetrakis(ethylmethylamido)titanium(IV) (TEMAT)를 전구체를 사용할 경우, SiO2 기판 위에 증착 온도 200° C로 증착한 TiNx의 성장 속도가 대략 0.5 nm/cycle 으로 포화되어 TEMAT과 NH3에 대한 자기제한적인 거동을 보였다. 하지만 증착 온도가 240° C일 때는 TEMAT 펄스 시간에 대한 성장 속도가 선형적으로 증가하였는데, 이는 TEMAT의 자기 열분해 온도가 230° C이기 때문이다.[91] TEMAT와 비슷하게 TDMAT도 전구체의 열분해에 의해서 자기제한적 거동이 방해받게 된다. Elam et al.은 Tetrakis(dimethylamido)titanium(IV) (TDMAT)와 NH3로 Si(100) 기판 위에 120° C로 증착한 TiN 막에서 TDMAT 펄스 시간 증가에 따라 성장 속도가 증가하다가 완전히 포화되지 않고 대략∼0.12 nm/cycle까지 느리게 증가하는 경향을 확인했다.[92] 이러한 이유에 대해 TDMAT 펄스 시간과 증착 온도 변화에 따른 TiN ALD의 활성화 에너지를 계산했을 때, 증착 온도가 120° C 일 때의 TiN ALD의 활성화 에너지인 0.12-0.13 eV가 TDMAT와 NH3를 사용한 저압 CVD의 활성화 에너지인 0.15 eV와 비슷하여 TiN의 ALD와 저압 CVD가 공통적인 속도 제한 단계를 갖기 때문에 자기제한적 성장으로 포화되지 않고 계속적인 성장이 발생한다고 보고하였다.[92] 또한, 증착 온도가 150° C 이상일 때 긴 TDMAT 펄스 시에 성장 속도가 포화되지 않고 계속적으로 증가하는 이유는 이때의 TiN ALD의 활성화 에너지인 0.57 eV가 TDMAT의 열분해 활성화 에너지와 비슷하기 때문에 긴 TDMAT 펄스에서 계속적인 성장이 발생하기 때문이다.[92] Musschoot et al.은 TDMAT 전구체에 공반응물로 N2, N2 플라즈마, NH3, NH3 플라즈마를 사용하여 증착 온도에 따른 질소 성분 공반응물의 ALD 거동을 보고하였다.[93] Si(100) 기판 위에 200° C 의 증착 온도에서 TiN ALD를 진행했을 때, NH3를 공반응물로 사용하여 증착한 TiN 막의 성장 속도인 0.06 nm/cycle에 비해 반응성이 높은 NH3 플라즈마를 공반응물로 사용한 경우에는 성장 속도가 0.08 nm/cycle로 더 높았다.[93] 이는 기판에 반응 사이트가 더 많은 기판-향상 성장을 하게 되면 성장 속도가 증가하는 것과 관련이 있다.[94] 또한, 이 연구에서는 증착 온도가 200° C 일 때 TDMAT의 펄스 시간이 증가함에 따라 성장 속도가 포화되는 경향을 보였지만, Elam et al.의 연구와 비슷한 결과로 펄스 시간이 긴 경우에는 성장 속도가 추가로 느리게 증가하는 것을 보였다.[93] N 계열 공반응물뿐만 아니라 H2 플라즈마를 사용한 경우에도 증착 온도 200° C와 플라즈마 파워 450 W로 증착한 TiN 박막에서 TDMAT 펄스 시간 증가에 따른 성장속도가 완벽하게 포화되지는 않았지만, 대략 TDMAT의 펄스 시간이 1 초일 때부터 0.41 Å/cycle의 성장 속도로 포화되는 경향을 보여 ALD의 자기제한적인 표면 흡착 반응이 일어남을 보여 주었다.[95] 또한, 250-350 W 플라즈마 파워로 증착한 TiN 막에서는∼200 μΩ cm에 해당되는 낮은 비저항 값을 얻을 수 있었다.[95]
2021년에 Lee et al.은 TiCl4과 NH3를 사용한 TiN ALD에 H2 S를 추가하여 증착 온도 400° C에서 성장 속도가 0.027 nm/cycle인 TiN 막을 증착하였다. H2 S를 추가함으로써 TiN 막 내에 염소 불순물을 20% 이상 감소시킬 수 있었고, 이로 인해 H2 S 펄스 전에 비해 비저항 값이 30% 이상 감소하여 198 μΩ cm의 저저항 TiN 막을 얻었다.[3] 열안정성이 좋은 TiCl4를 사용한 기존 CVD 와 ALD 공정에 비해 비교적 저온인 400°C에서 증착하여 DRAM 커패시터와의 호환성을 가질 수 있었으며, 염소 불순물을 감소시켜 TiN의 비저항을 줄일 수 있는 새로운 접근을 통해 TiCl4 전구체 사용의 가능성을 높일 수 있었다. 최근에 Kuo et al.은 Ti 전구체로 TiCl4와 유기 금속 전구체(TDMAT, Tetrakis(diethylamino) titanium(IV) (TDEAT), TEMAT)를 사용하고 공반응물로 anhydrous hydrazine (N2 H4)을 사용하여 SiO2(300 nm)/Si 기판 위에 ALD한 TiN에서 공정 조건 변화에 따른 성장 속도와 비저항 값을 측정하였다.[96] 이 중 TiCl4을 사용하였을 때 500° C 증착 온도로 증착한 TiN에서 1.95 Å/cycle의 성장 속도와 89.08 μΩ cm의 매우 낮은 비저항 값을 얻어 향후 전도 특성을 갖는 TiNx ALD를 증착하기 위한 전구체와 공반응물의 선택폭을 넓혔다.[96]
2.4 ZrNx ALD
ZrN은 지르코늄 (Zirconium)과 질소 (Nitrogen)로 구성된 화합물로, 금속 질화물로 분류되며 rock-salt 구조를 가져 구조적인 안정성이 있는 물질이다. Zr3+ 양이온과 N3- 음이온의 배위수는 동일하게 6이며, 팔면체 자리를 형성한다. ZrN은 우수한 화학적 및 물리적 특성으로 주목받는 소재이며, 특히 높은 화학적 안정성 및 열적 안정성, 높은 경도 및 내마모성을 갖추고 있어 외부 환경에 저항성이 높은 얇은 박막을 만드는 데 적합하다.[97] 또한 낮은 전기저항, 극저온에서의 초전도 특성, 높은 내식성을 가지고 있다.[98,99] 위의 특성에 따라 ZrN 박막은 우수한 기계적 특성, 높은 화학적 열적 안정성을 가지며 기계, 화학, 및 생물의학 분야의 보호 코팅에 사용하기 적합하고,[97,99] 또한 부식을 방지하기 위한 코팅 등의 용도로 사용된다.[100] 이러한 ZrN 박막은 sputtering[15,97,101], CVD[42,102], ALD[46,103,104] 등의 방법으로 증착되어 왔으며 본 논문에서는 ALD 공정에 대해 집중적으로 다룰 예정이다.
2015년 캐나다 앨버타 대학의 Muneshwar, Cadien은 TDMAZr (Tetrakis(dimethylamido)zirconium(IV)) 및 포밍 가스 (5% H2 + 95% N2) 플라즈마를 사용한 ZrN 박막의 플라즈마 PEALD에 대해 보고하였다.[105] ZrN 박막이 성장된 기계의 도면은 Fig. 1.a 에 있다. 자기제한적 성장을 위한 ALD 최적의 매개변수 결정을 위해 기판 온도, TDMAZr 펄스량, 플라즈마 노출 시간, 전구체 펄스 이후 Ar 퍼지 시간, 플라즈마 노출 이후 Ar 퍼지 시간 등을 변화시켰으며, 추가적으로 기판은 SiO2, 증착 온도는 150° C, 플라즈마 파워는 600 W이었고, 이러한 조건들을 통해 최적의 성장 포화 조건을 보고하였다. 자기제한적 성장 조건 하에서 최적의 기판 온도 (T sub) 및 증착 주기 매개변수 (t1∼ t4)를 찾기 위해 증착 실험은 추측 주기 (guess cycle)를 설정하여 모든 실험 세트에서 단일 테스트 매개변수를 변화시키는 방식으로 진행되었다(Fig. 1.b), (Table. 4). 결론적으로 위의 실험을 통해 정해진 매개변수로 0.10 nm/cycle의 일정한 성장 속도를 얻을 수 있었고, 실험 횟수를 줄여 ALD 프로세스 개발을 빠르게 진행할 수 있도록 도울 수 있다.[105] 덧붙여 추후 동일한 TDMAZr 전구체와 포밍 가스 (5% H2 + 95% N2) 플라즈마를 사용하여 PEALD로 ZrN 박막을 증착할 때, ALD 밸브 내에서의 전구체 응축 현상을 서술하였다. 이 실험의 공정조건은 (Table. 5)에서 볼 수 있듯 위 실험과 다른 기판 Si (111)/ SiO2를 사용했다는 점을 제외하면 동일하다. 전구체가 응축된 상태로 ALD가 진행이 되면 응축된 전구체가 지속적으로 반응기 내로 유입되어 ALD 공정 동안 non-ALD 성장 성분을 생성한다. Muneshwar, Cadien은 다른 매개변수는 고정한 상태에서 온도를 75° C에서 95° C로 증가시켰을 때 밸브 내의 응축 현상이 사라졌고, 성장 속도와 전기저항(ρ)이 각각 0.10 nm/cycle 에서 0.07 nm/cycle로, 560 μΩ⋅ cm에서 350 μΩ⋅ cm로 감소하였음을 보고했다. 결론적으로 Muneshwar, Cadien은 ALD 밸브 온도가 ALD 막의 성장과 특성에 직접적으로 영향을 미친다는 결론을 내렸고, 좋은 품질의 ALD 박막을 얻기 위해서는 ALD 밸브 온도의 선택이 매우 중요하다는 것을 보고했다.[106]

a. ALD150LX reactor design schematic highlighting TDMAZr and forming gas delivery lines and the M2000DI spectroscopic ellipsometer for in-situ ALD growth characterization. b. Precursor and plasma pulsing sequence for a ZrN PEALD cycle.[105] Reprinted with permission from [Triratna Muneshwar, Ken Cadien; Low temperature plasma enhanced atomic layer deposition of conducting zirconium nitride films using tetrakis (dimethylamido) zirconium and forming gas (5% H2 + 95% N2) plasma. J. Vac. Sci. Technol. A 1 May 2015; 33 (3): 031502.]. Copyright [2024], American Vacuum Society
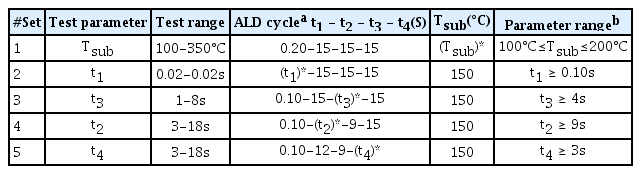
ALD process development for self-limiting ZrN growth with respect to, substrate temperature (T sub), TDMAZr pulse (t1), Ar purge (t2), plasma exposure (t3), and Ar purge (t4). From the characteristic ALD growth curves with single variable parameter (*), its optimum range for self-limiting growth is determined and used in following experiments.[105] Reprinted with permission from [Triratna Muneshwar, Ken Cadien; Low temperature plasma enhanced atomic layer deposition of conducting zirconium nitride films using tetrakis (dimethylamido) zirconium and forming gas (5% H2 + 95% N2) plasma. J. Vac. Sci. Technol. A 1 May 2015; 33 (3): 031502.]. Copyright [2024], American Vacuum Society
또한 2019년 미국 일리노이주의 아르곤 국립 연구소의 Bhattacharya et al은 U-Mo 분말에 ALD를 통한 나노 결정질 ZrN 박막 개발을 보고하였으며,[103] 이는 악티나이드 재료 코팅에 ALD를 사용한 첫 번째 사례이다. 그동안 ZrN 박막은 주로 PVD와 CVD를 통해 증착되었으나, 공정 진행 중 박막의 균열이나 박막이 박리되는 상황이 발생하였고 이러한 문제의 발생 방지를 위하여 대체 코팅 기술인 ALD가 고려되었다. 위의 이유에 따라 개발된 ALD ZrN 코팅은 핵 환경에서 사용할 확산 장벽으로 선택되었으므로 안정성을 관찰하기 위해 방사선 환경에서의 박막의 거동을 연구하는 것이 중요했다. 그러 하여 Bhattacharya et al.은 TDMAZr 전구체와 NH3 공반응물을 사용하여 245° C의 증착 온도에서 증착했고, 0.11 nm/cycle의 균일한 성장 속도를 얻을 수 있었다. 이온 조사 (Ion Irradiation)되지 않은 ALD ZrN 박막과 이온 조사된 ALD ZrN 박막에서 전자 회절의 방위각 적분을 관찰했을 때 (111)과 (200)의 피크가 이온 조사 후 약간 날카로워졌음을 알 수 있었으며 이는 결정 조대화 (grain coarsening)를 나타낸다.[103] 결정 조대화가 일어난다면 물질의 기계적 강도 감소 및 화학적 안정성에 변화를 줄 수 있기 때문에 조대화가 되지 않는 것이 중요하다. 위 실험에서 ALD ZrN 코팅은 81 시간 동안, 이온 조사 온도보다 훨씬 높은 245° C에서 증착되었기 때문에 온도는 조대화에 어떠한 영향도 주지 않는다는 것을 알 수 있다.[107] 만약 온도만으로 결정이 조대화될 수 있었다면 증착된 샘플에 대해 수행된 단면 연구에서 기판에서 상부 표면까지 결정 크기의 눈에 띄는 구배가 관찰되었어야 한다. 그러나 구별 가능한 입자 크기 구배가 관찰되지 않았기 때문에 결국 이는 온도만으로는 결정이 조대화될 수 없음을 나타내며, 동시에 높은 온도의 방사선 환경에서 박막의 거동이 안정하다는 것을 입증하였다.[103] 현재까지 ZrN 증착을 위한 물리적 증착 및 화학적 증착 기술과 비교하여, ALD에 의한 ZrN 성장에 관한 논문은 매우 적게 보고되었다. 그 이유는 각 논문에서 증착 과정을 똑같이 재현할 수 있을 만큼 세부적으로 진행 절차와 매개변수 등을 설명하지 않아 발생하는 최종 결과값 차이에 의한 것으로 예상된다.[108] 한 층씩 증착하여 CVD 및 PVD보다 더 정교한 증착이 가능한 ALD를 더욱 다양한 분야에 접목시킬 수 있도록 더 많은 연구가 진행되어야 할 것으로 보인다.
2.5 SiNx ALD
SiNx는 기계적, 광학적, 화학적, 전기적으로 우수한 특성을 가지고 있어 태양광, 반도체 등 다양한 응용 분야에 널리 사용되는 소재이다. 넓은 밴드 갭 (∼5.2 eV)[109]으로 인해 광전자 소자 응용에 사용되며, 높은 물 불투과성[109]을 가지고 있어 유기 발광 다이오드(OLEDs)의 장벽층의 잠재적 후보로 떠올랐다. SiNx는 내화물[110], 반사 방지 코팅 막[111], 태양 전지의 패시베이션 층[112], 디스플레이의 encapsulation layer[113], 확산 장벽[114], 게이트 유전체[115], 스트레스 라이너[116] 등에 활용되었다. 기존의 CVD[17]나 LPCVD[22]는 일반적으로 700° C 이상의 높은 증착 온도에서 이루어져 왔으며, 극초고밀도 집적 회로 (ULSI) 기술에서 많은 thermal budget을 필요로 하였다. 이를 개선하기 위해 도입된 PECVD[23]는 400° C 이하의 저온에서 필름 성장을 가능하게 했지만, 기존 CVD에 비해 낮은 에칭 저항과 단차 피복성을 보여 주었다. 그 결과, 낮은 thermal budget으로 고품질의 등각성이 우수한 SiNx 박막을 증착하기 위해 ALD가 도입되었다. 현재까지 thermal ALD와 PEALD를 활용한 다양한 연구 결과가 성공적으로 얻어지고 있으며, SiNx ALD는 차세대 ULSI 기술을 확장하는 데 필수적인 기술로 간주되고 있다.
2014년 Jang et al.은 ALD에 플라즈마를 도입하면 기존의 불순물 문제를 효과적으로 해결할 수 있지만, 이온 충격에 의한 기판 손상이 발생한다는 문제에 주목하였다. 이에 대응하여 remote plasma atomic layer deposition (RPALD)를 도입하여 플라즈마에 의한 기판 손상을 최소화하고, 이 방법으로 얻은 SiNx 박막의 특성을 조사하였다. 이때 전구체로 trisilylamine(TSA)와 NH3 플라즈마를 사용하였으며, Si(100) 기판에서 100 W의 플라즈마 파워를 인가하여 150-350° C의 온도 범위에서 공정을 진행하였다. 증착된 SiNx 박막은 다양한 온도에서 Si3 N4로 화학양론적인 특성을 나타냈으며, 증착 온도가 250° C에서 350° C로 증가함에 따라 굴절률은 증가하는 반면, 수소 함량은 13.4 at%에서 8.1 at%로 감소하는 것을 관찰하였다. 특히 고온에서는 결함 밀도가 변화하며, 수소 함량 감소로 인해 모든 트랩 밀도가 증가하는 현상이 확인되었다. RPALD에 의해 증착된 SiNx 박막은 전하 트랩 플래시 메모리 응용을 위한 결함 밀도를 조절하기 위해 증착 온도를 조절하는 제어 방법을 제시하였다.[117]
디바이스 초소형화 및 설계 규칙의 복잡성이 지속적으로 증가함에 따라, high-k 금속 게이트 트랜지스터의 게이트 스페이서 막은 우수한 에칭 저항과 높은 등각성을 갖추어야 한다.[118] 또한 스페이서는 500° C 이하의 낮은 온도에서 증착되어야 하며, 동시에 필름의 품질은 높게 유지되어야 한다. 이러한 요구 사항에 부합하기 위해 SiNx 박막 증착에는 ALD가 적합하다. 일반적으로 SiNx의 ALD에는 전구체로 chlorosilane (e.g., SiCl4, SiH2 Cl2, Si2 Cl6, Si3 Cl8)이 사용되고, 공반응물로는 NH3, NH3 플라즈마, 또는 N2 H4가 사용되어 왔다. 그러나 chlorosilane을 사용하는 공정은 비교적 높은 증착 온도를 필요로 하여, 이를 극복하기 위해 SiH4와 N(SiH3)3과 같은 염소가 없는 전구체를 사용하는 PEALD 공정이 도입되었다.[117,119] 2015년 Knoops et al.은 bis(tert-butylamino)silane (BTBAS)와 N2 플라즈마를 활용한 새로운 ALD 공정을 개발하였다.[26] PEALD 공정은 c-Si 기판을 사용하고 600 W의 플라즈마 파워를 인가하여 25-500° C의 온도 범위에서 진행되었다. 이 공정은 모든 온도에서 성장 지연 없이 선형 성장을 나타내며, 온도 증가에 따른 성장 속도의 감소를 관찰하였다(Fig. 2). LPCVD 및 고온 thermal ALD를 대체하기에 적합한 300-500° C의 증착 온도에서 고품질의 SiNx를 얻었으며, 500° C에서는 Si3 N4에 가까운 조성을 관찰하였다. 400° C 이상에서 증착한 필름은∼5%의 낮은 수소 함량을 가지고 있어∼1 nm/min로 낮은 습식 식각 속도를 보여주었고, 이는 700° C 이상에서 LPCVD를 통해 증착한 Si3 N4와 유사하다고 보고되었다. 향후 연구에서는 SiNx 필름과 ALD 공정의 적합성을 더욱 탐구하고, 성장 메커니즘에 대한 더 깊은 이해의 필요성을 제시하였다.[26]

Growth per cycle (GPC) as a function of the precursor dosing time for a table temperature of 100° C, 200° C, and 500° C. The GPC was determined using a 3 s plasma exposure time. The lines serve as a guide to the eye.[26] Reprinted (adapted) with permission from Harm C. M. Knoops, Eline M. J. Braeken, Koen de Peuter, Stephen E. Potts, Suvi Haukka, Viljami Pore, and Wilhelmus M. M. Kessels ACS Applied Materials & Interfaces 2015 7 (35), 19857-19862. Copyright 2024 American Chemical Society.
2016년 Park et al.은 Si 전구체로 silylamine 화합물인 bis(dimethylaminomethylsilyl)-trimethylsilyl amine (C9 H29 N3 Si3, DTDN2-H2)을 채택한 PEALD 연구를 보고하였다. 전구체로 DTDN2-H2와 N2 플라즈마를 사용하였고, 100 W의 플라즈마 파워를 적용하여 250-400° C의 온도 범위에서 Si(100) 기판에 실리콘 질화물을 증착하였다. DTDN2-H2는 기존에 Si 전구체로 쓰여왔던 TSA의 열 안정성을 향상시키기 위해 SiH3 그룹을 dimethylaminomethylsilyl 또는 trimethylsilyl 그룹으로 대체하여 설계되었다. TSA의 화학구조를 기반으로 재분배, 아미노 치환, lithiation 및 silylation 반응을 통해 합성되었으며, 결합 해리 에너지가 낮고 증기압이 충분하여 전구체로 적합하다. Si 전구체로 BTBAS를 사용한 PEALD보다 DTDN2-H2로 증착한 SiNx에서 0.36Å/cycle로 더 높은 성장 속도로 관찰되었고, 250-400° C의 ALD 온도 창 내에서 탄소 함량이 발견되지 않았다. [N]/[Si] 비율은 300° C에서 0.98, 400° C에서 0.99로 관찰되었으며 이는 700° C에서 LPCVD를 통해 증착한 필름과 거의 동일한 값이다.(Fig. 3) 100 W의 RF 파워에서 고품질의 필름을 얻었으며, 탄소 불순물의 증착으로 인해 RF 파워가 증가함에 따라 트랩 밀도와 습식 식각 속도가 증가한다고 보고하였다. 본 연구의 PEALD 필름은 종횡비 5.5의 트렌치 패턴 웨이퍼에서 각각 80%와 73%의 좋은 바닥 및 측벽 coverage를 나타내어, SiNx의 Si 전구체로서의 DTDN2-H2의 가능성을 보여 주었다.[120]
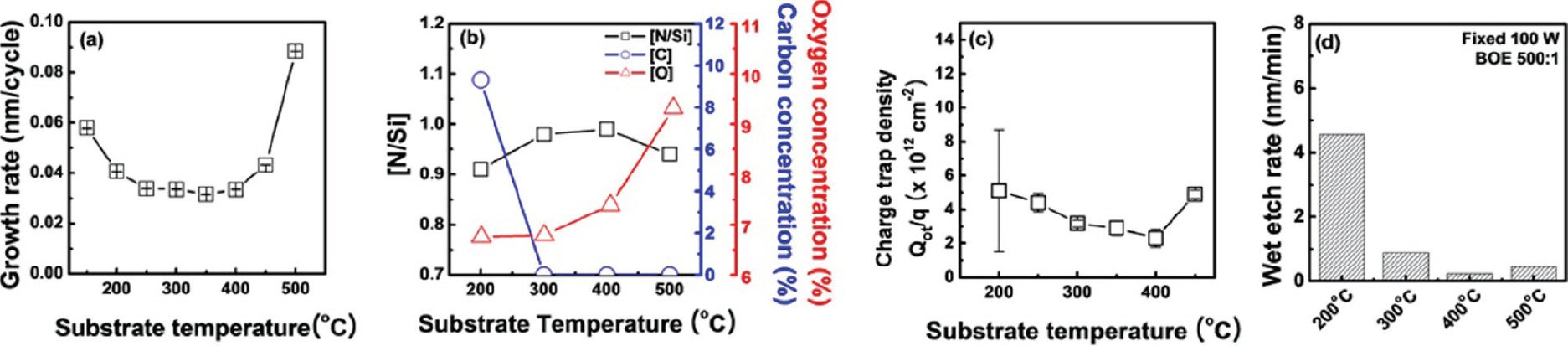
Effect of deposition temperature. PEALD silicon nitride films were prepared with a RF power of 100 W at various deposition temperatures: a. growth rate, b. concentration ratio of nitrogen to silicon ([N]/[Si]) and carbon concentration, c. charge trapped density, and d. wet-etching rate in a diluted HF solution.[120] Reprinted (adapted) with permission from Jae-Min Park, Se Jin Jang, Luchana L. Yusup, Won-Jun Lee, and Sang-Ick Lee ACS Applied Materials & Interfaces 2016 8 (32), 20865-20871. Copyright 2024 American Chemical Society
3. 결론
본 논문에서는 주요 질화물 박막 소재로 알려진 하프늄 질화물, 알루미늄 질화물, 타이타늄 질화물, 지르코늄 질화물, 실리콘 질화물의 전구체 및 공반응물에 따른 전기적, 구조적 특성을 탐구하였으며, ALD 기술에 대한 최신 동향에 대해 고찰하였다. 고찰 결과, ALD를 이용한 질화물 박막 증착은 기존의 증착 방법에 비해 낮은 온도에서 고품질의 박막 형성과 나노 스케일에서의 뛰어난 등각성을 제공함이 확인되었다. 특히, ALD는 미래 나노 전자 소자 및 기술 분야에서 핵심 공정 기술로써 중요한 역할을 할 것으로 예상되고 있다. 고품질의 박막 합성을 위한 연구는 계속 진행 중이며, 각 소재에 대한 ALD 적용이 효과적인 성능을 나타내고 있다. 특히, TiNx ALD에서는 H2 S를 공반응물로 추가하여 비저항 값을 감소시키고 전도 특성을 개선하는데 기여하였으며, TiCl4 전구체의 사용 가능성을 탐구하여 전구체 및 공반응물의 다양성을 확장하였다. SiNx 분야에서도 ALD에 적합한 특성을 갖는 새로운 전구체를 개발하여 고품질의 박막을 얻었으며, 향상된 공정 개발을 위해 노력하고 있다. 최근에는 strain의 영향으로 강유전성을 갖는 HfNx 박막을 합성함으로써 MFSFET에서 강유전층으로의 적용 가능성을 시사하였다. AlNx 박막 또한 최근 이종 접합에서의 격자 불일치에 기반한 강유전성 연구 결과가 보고되었다. 이는 ALD로 합성된 HfNx 및 AlNx 박막도 강유전성을 얻을 수 있음을 시사하며, 새로운 기초 및 연구의 필요로 인해 해당 공정 개발에 중점을 두어야 할 필요성이 제기되었다. 현재까지는 ALD를 이용한 ZrNx 박막 합성에 대한 활발한 연구가 부족하여, 해당 분야의 공정 개발에 더욱 박차를 가해야 할 것으로 보인다. 종합적으로, ALD를 통한 질화물 박막의 연구는 새로운 기술과 응용 분야에서의 발전을 촉진할 것으로 기대되며, 이를 통해 나노 기술 및 반도체 산업의 지속적인 발전에 기여할 것으로 기대된다.
References
Biography
⊙⊙ 이 자 영
⊙ 2019년 – 현재 충남대학교 신소재공학과 학사과정
⊙⊙ 최 보 윤
⊙ 2022년 충남대학교 신소재공학과 학사
⊙ 2022년 – 현재 충남대학교 신소재공학과 석사과정
⊙⊙ 안 준 혁
⊙ 2020년 – 현재 충남대학교 신소재공학과 학사과정
⊙⊙ 전 나 리
⊙ 2016년 Northwestern University Ph.D. Materials Science and Engineering
⊙ 2019년 Argonne National Laboratory Postdoctoral Fellow
⊙ 2023년 충남대학교 신소재공학과 조교수
⊙ 2023년 – 현재 충남대학교 신소재공학과 부교수